The DZOMUSA took place from the 3rd to 4th of December, with attendees from all over the zero-emissions off-highway machinery industry coming together in Chicago, Illinois at the Donald E. Stephens Convention Center. The two day conference had a wide and comprehensive agenda that involved dozens of presentations from expert speakers, panel discussions, fireside chats workshops and networking breaks.
Attendees of our AOMT track had the opportunity to hear about the most relevant challenges, innovations and opportunities related to cutting-edge developments, autonomous machines, AI and deep learning, and advanced sensor technologies, software, and data management, alongside the regulatory and ethical considerations that accompany these innovations
This article will provide a session recap for those who didn’t get the chance to attend and serve as a reminder for those who attended.
Day One
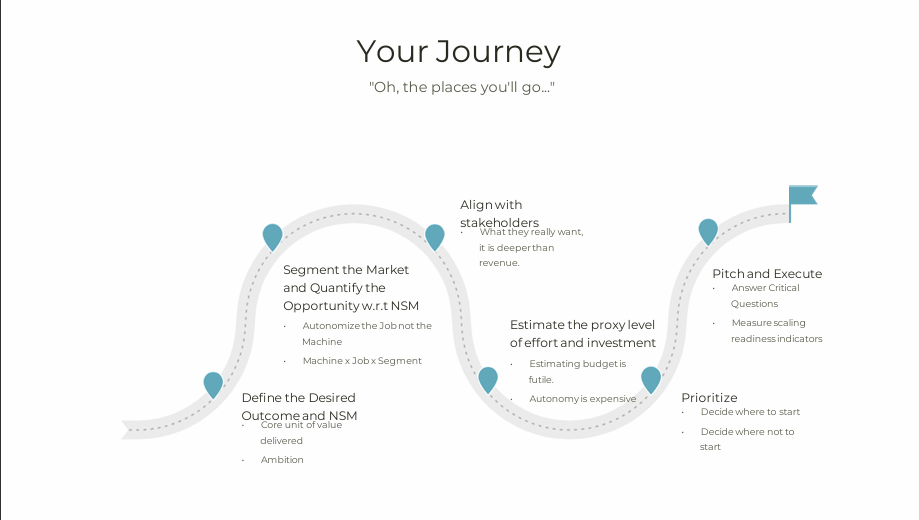
The Enterprise Autonomy Journey: A playbook
Nir Rikovitch, Director of Product Management at Blue River Technology
Nir’s keynote was a guided journey through the process of autonomy, with the guiding ambition of delivering differentiated solutions to off-road industries that meaningfully ease the labour shortage, leveraging our strength in technology integration. Autonomy is approached with the mindset that rather than autonomizing a machine, we’re autonomizing a job in a production system. Maximum customer value with a minimal level of effort (LOE) leads to the highest return on investment. Companies should start with low LOE products to minimise initial investment, get to market quickly, expand to a new job and then expand a job to be automated into a new production system. He concluded that scaling or expanding requires organisational readiness, product readiness, product-channel fit and product-market fit.
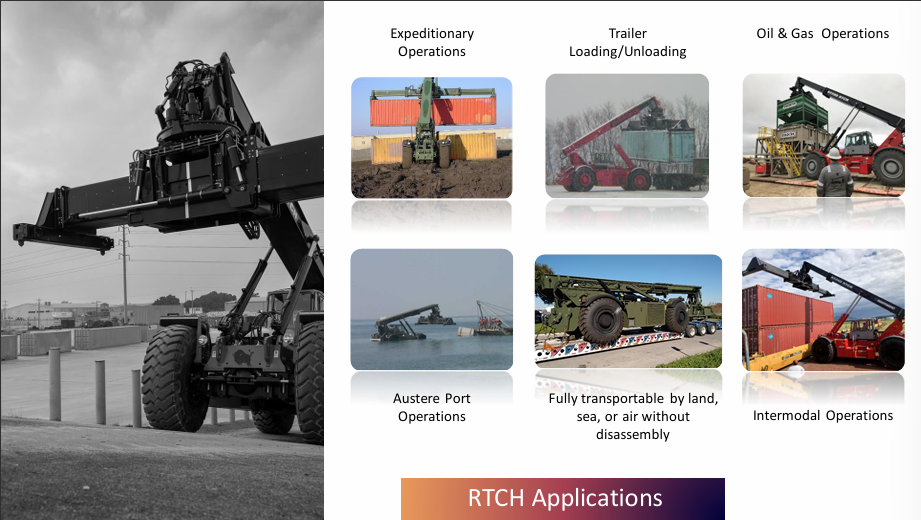
Navigating the Autonomous Roadmap: Challenges & Opportunities
Cody Parvin, Director of Customer Solutions at Independent Rough Terrain Centre (IRTC) LLC
Cody discussed the autonomy journey of IRTC, with their Rough Terrain Container Handler (RTCH) becoming semi-autonomous in the future with the ability to conduct container operations, detect obstacles preventing placement or causing collision and target functions like using tophandlers. Existing sensor precision and margin of error are sufficient for base machines but not for autonomous systems as data transmission speed and timing are critical for efficient container engagements and placements. Government customers’ high-volume container movement and focus on soldier safety drive strong potential for full autonomy, whilst commercial customers’ preference for multi-purpose functionality reduces the need for full autonomy. Autonomous solutions must balance rugged terrain durability with cost efficiency to encourage widespread adoption.
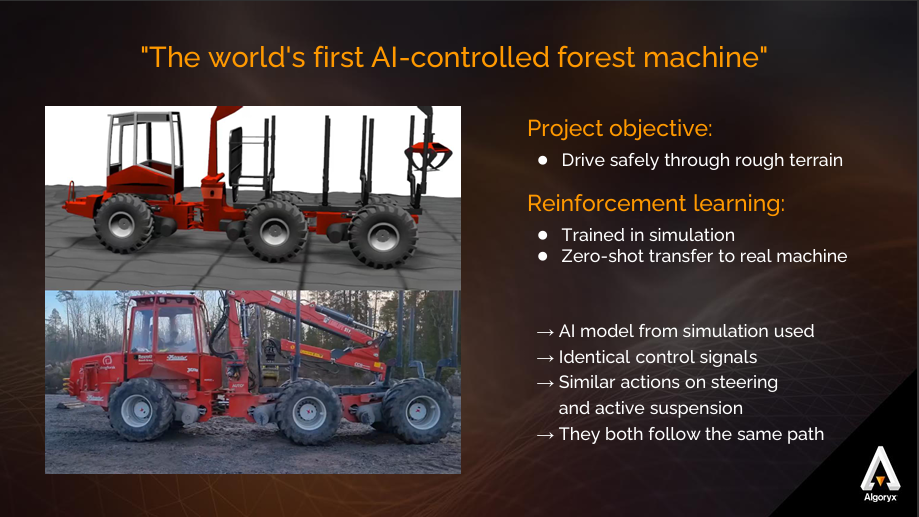
Bridging the Simulation to Reality Gap in Offroad Autonomy
Urban Wikman, Business Director, and Hugo Borjessen, Senior Technical Business Director, at
Algoryx
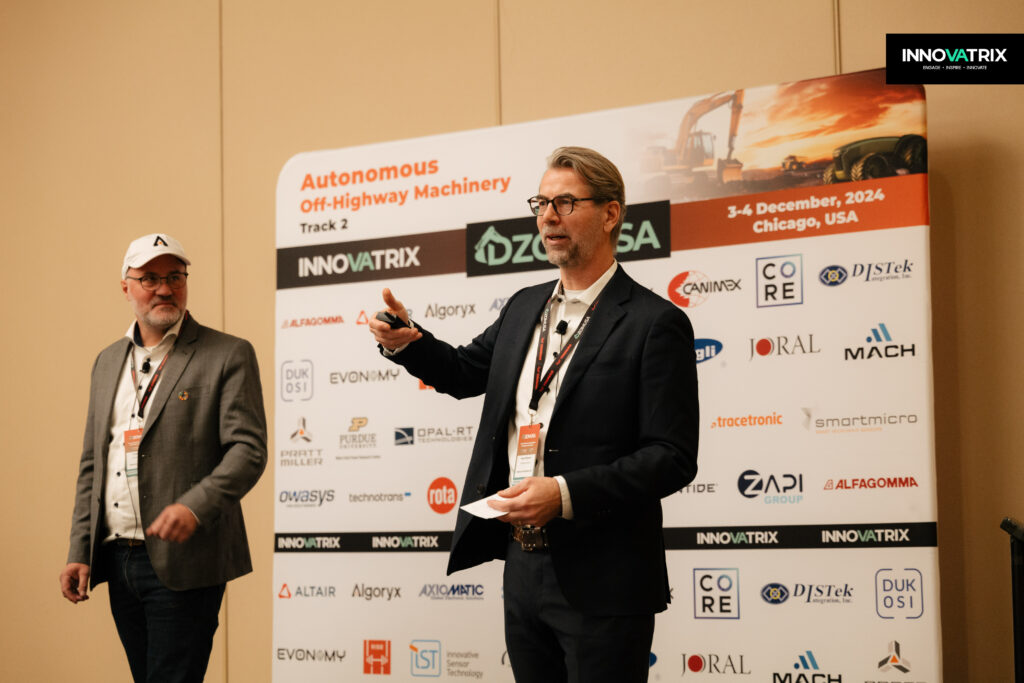
The team from Algoryx discussed simulating complete systems with modelling and AI training to create a digital proving ground. Digital twins, sensors, control systems, tests and scenarios and AI models are vital to research and development and can be used to create the simulation of the complete system. The AI prediction model helps the operator optimise the load cycle by finding the best attack point by using loaded mass, cycle time and energy data, optimising the loading performance. The AI model is 97% accurate in 4.5 ms and is able to run long-horizon prediction like how to maintain optimal pile shape, optimize mass/hour and optimize mass/kwh.
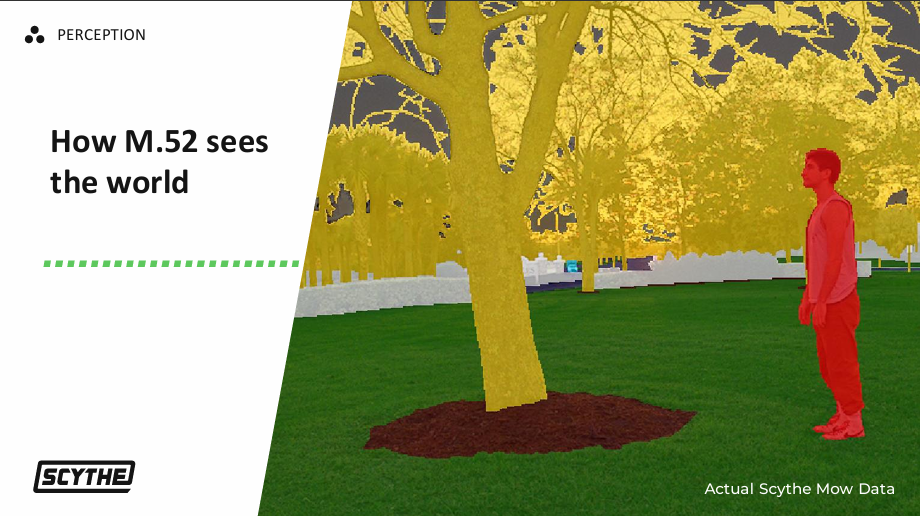
Off-roading Robots: Bringing Autonomy to Unstructured, Outdoor Environments
Jack Morrison, Co-Founder and CEO at Scythe Robotics
Jack shared the critical considerations for off-road autonomy – durability, perception and computation. The use of electric power increases durability as traditional mowers are expensive and unreliable whilst electric mowers eliminate maintenance and have a fraction of the moving pieces. Electric autonomous mowers can be engineered for extreme outdoor conditions with a ground-up, in-house design using reinforced and well-protected sensors and commercial-grade materials with manual abilities in all terrains. Software language can optimise processing performance, with Rust being the ultimate solution as its fast execution and high safety makes it ideal.
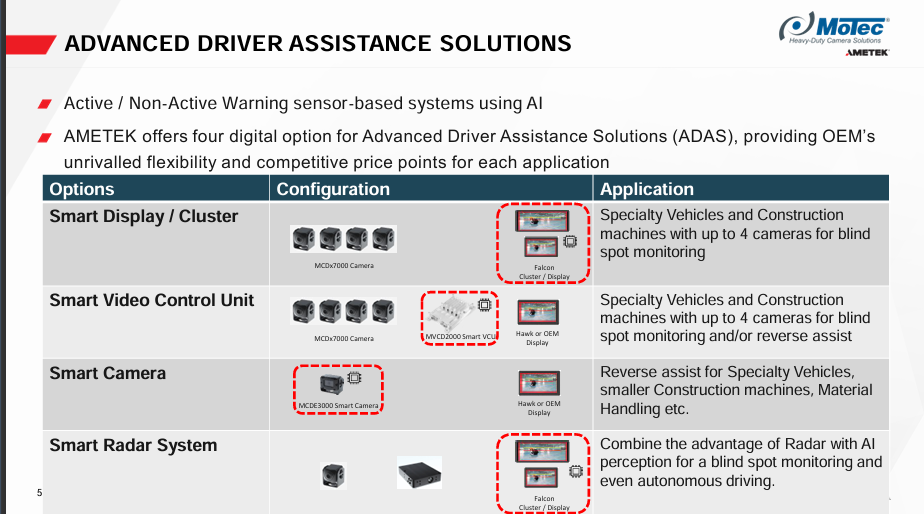
Flexible approach of camera-based driver assistance systems for mobile machinery
Dr. Stefan Wirtz, Director Engineering at Motec GmbH – Ametek
Higher productivity demands are compromising safety and billions are lost annually due to expensive accidents. Advanced Driver Assistance Solutions (ADAS) have active/non-active warning sensor-based systems using AI. AMETEK offers four digital options for ADAS providing OEMs unrivalled flexibility and competitive price points for each application. AI data mostly only shows city scenarios and there is limited available data which requires doing annotation. Using humans to fill the data gap by using self-captured videos and a VIT to extract information allows for advanced scene understanding, The extracted data can create relevant model scenarios that can be used for hazard analysis.
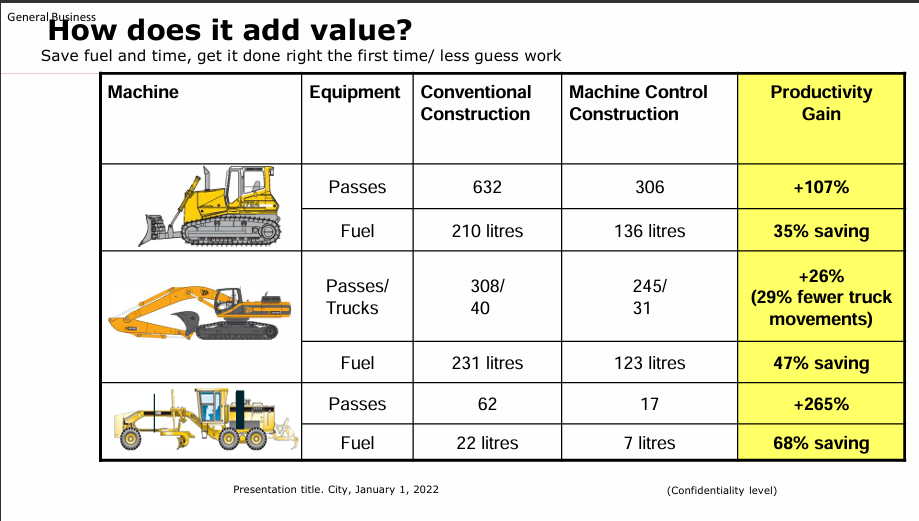
GNSS and machine control systems
Kevin Scotese, Global Director – Digital & Innovation Strategy at CNH Industrial
GNSS and machine control are increasing productivity and improving costs, timing, safety and quality, pushing modern construction management into a completely new era. GNSS and machine control allow users to save fuel and time, less guesswork and get it right the first time. A 3D jobsite journey begins with a modelling project after submitting a bid, localising the site and importing a 3D model. GNSS can be used in perception, positioning control and AI by taking the output of perception, utilising GNSS with a model, localising the machine in the world and the attachment to the material. The material input is 3% lower, labour costs are 35% lower and staking costs 75% less when using 3D solutions
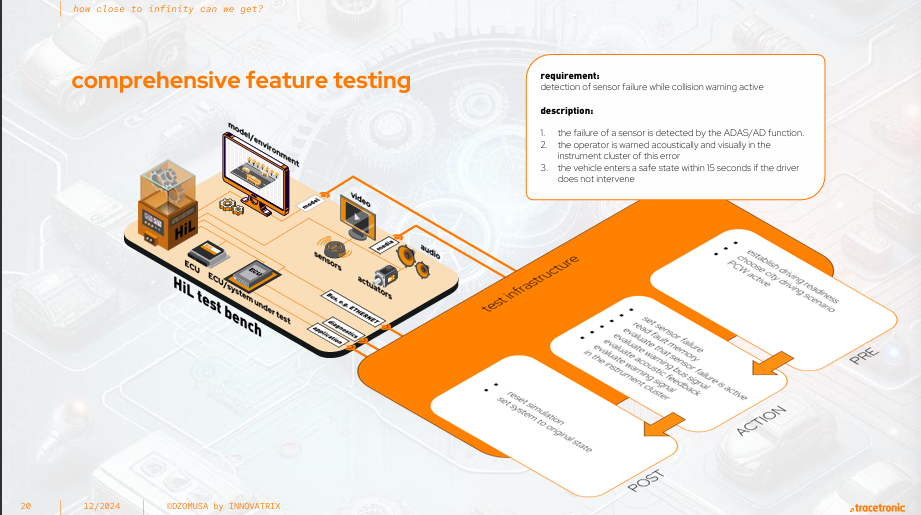
Shifting Left – Efficient, Automated Software Testing for Complex, Autonomous Machines
Felix Mueller, General Manager at Tracetronic
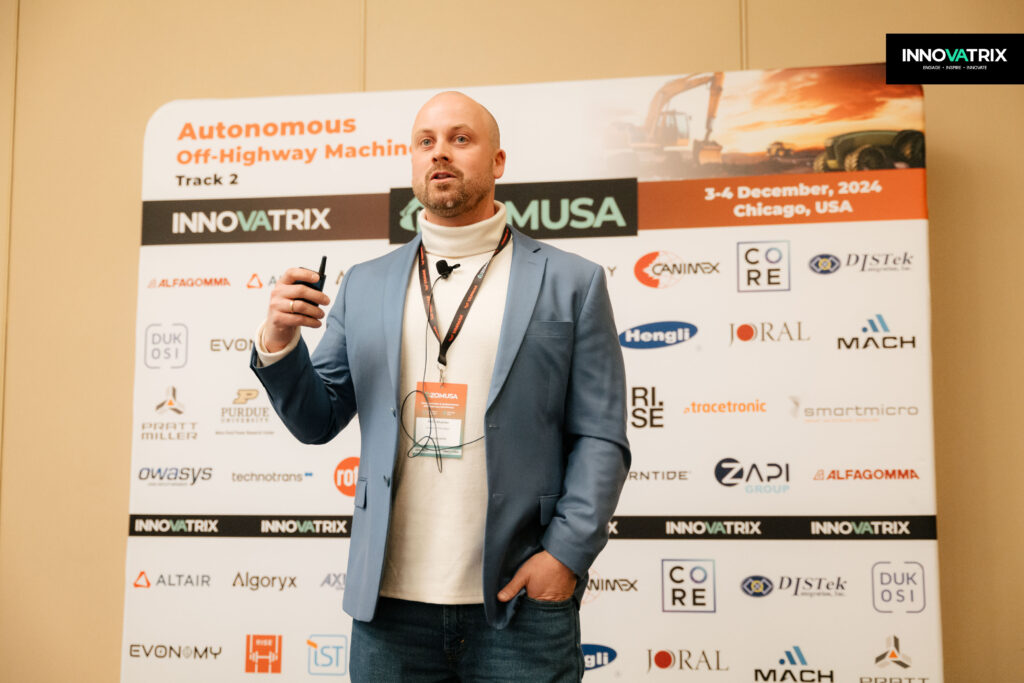
Shifting left refers to using testing in a virtual space in earlier stages of development to ensure less work in the final stages which is often costly. The testing is cloud-based so there are lower costs for error discoveries and lower costs of additional resources later. By shifting left projects, costs are lower, the software quality is higher, there is a quicker response to customer demands and feedback and a greater test quantity. Organisations can shift left by using automation, standardisation, reusability, creating fast feedback loops and perfect environments and tools.
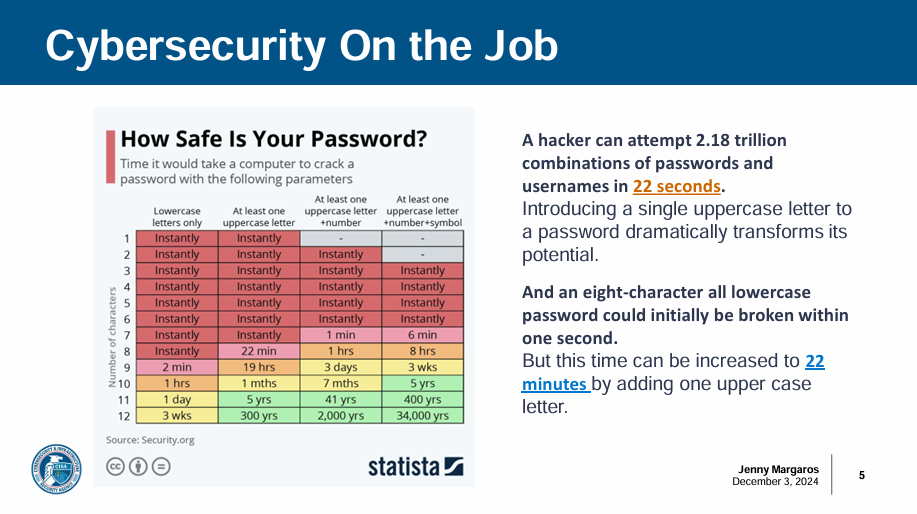
Cybersecurity threats and the vulnerabilities inherent in connected systems and machines
Jenny Margaros, Section Chief, Critical Manufacturing Section at the U.S. Department of Homeland Security
Jenny discussed the importance of cybersecurity as it causes direct and indirect costs to increase as any company is a reachable connected, target. Cybersecurity should be as important as physical security, prioritised by working with your IT and OT teams and reporting issues. She also introduced the CISA cybersecurity program, products and services and their network of regional offices. They offer protective security advisers, cybersecurity advisors and access to the product events service website.
Key enablers for off-highway autonomy
Dr. Jake Steiner, Autonomy Lead at Pratt Miller
Autonomy aims to achieve more work with the same number of workers. Autonomous vehicles can be integrated into existing work progresses and in controlled environments where restrictions are less restrictive. The key enablers for off-highway autonomy is a system architecture for scalable and modular autonomy implementations, the use of mapping and localisation in off-highway environments and using a “Crawl, Walk, Run” development methodology (proof of concept, prototype and pilot).
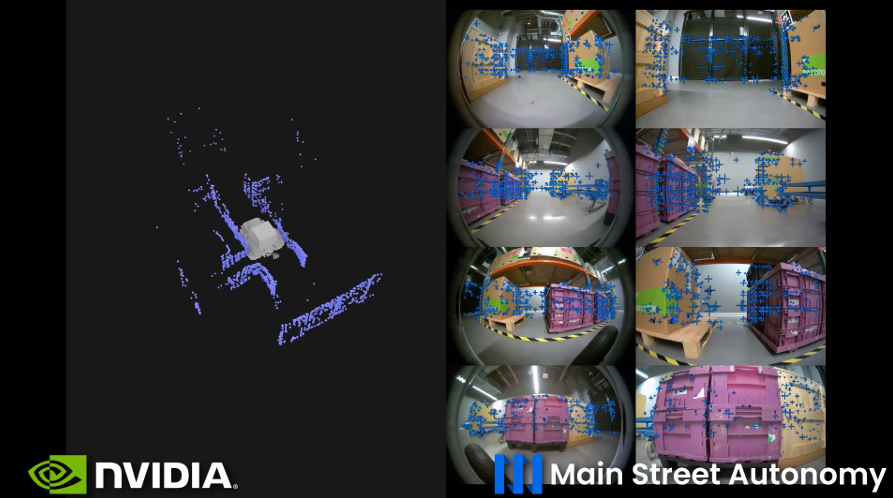
Perception Based Localization
William Sitch, Chief Business Officer at Main Street Autonomy
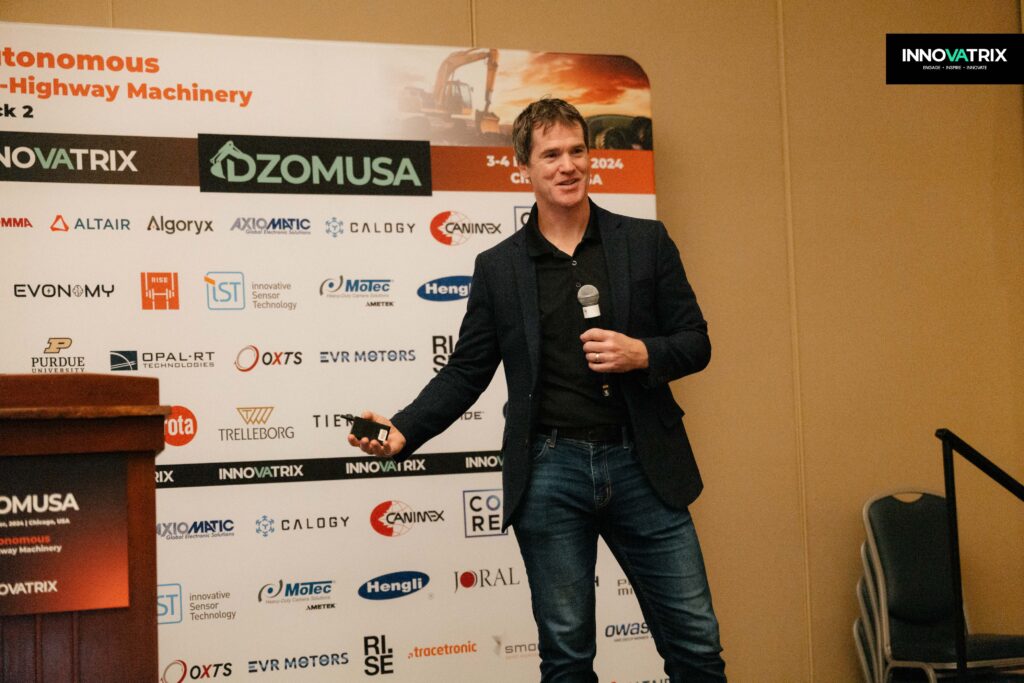
William began his first of two presentations with the value proposition of robots. Robots deliver value by being in one place at a time. Their deployment is limited by robot capability, GNSS is unreliable and downtime can be expensive. A reliability of 90% limits deployments and drives costs, making good localisation and mapping a key component of increasing the value of robots.
Day Two
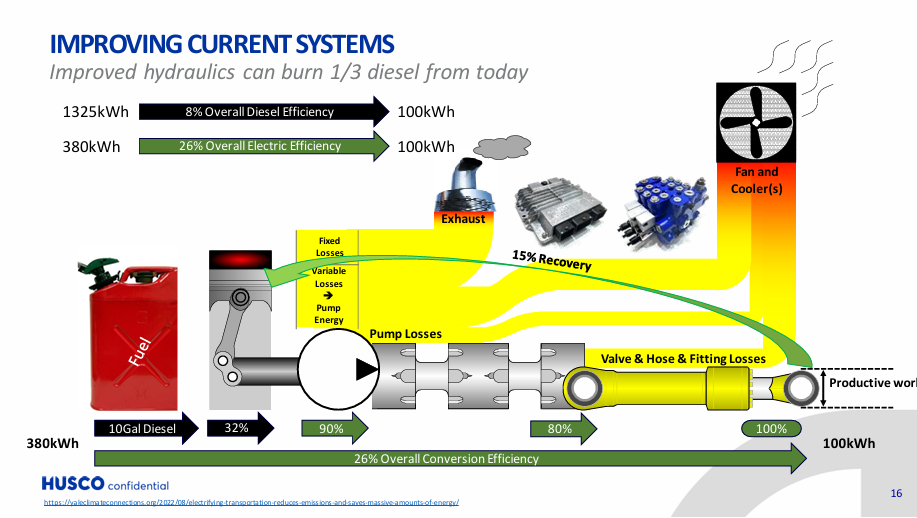
Hydraulic Control Systems: Empowering the Future of Efficiency and Automation
Ben Holter, Director – Digital Systems at Husco
Ben started his presentation with the question of how to improve hydraulics. By using condition-based controls, hydraulics can have multiple inputs and can recover potential with multiple different outputs. Independent metering, multi-chamber, multi-rail and multi-pump electrohydraulics can be used as an enabler for automation and efficiency. An electrohydraulic system approach also enables high level control and defines software.
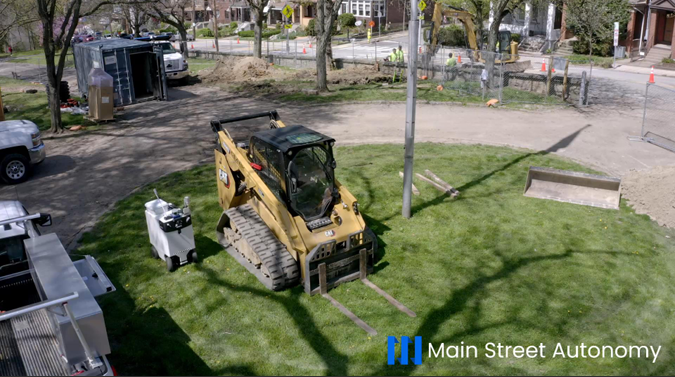
Sensor Technology for Localization and Mapping
William Sitch, Chief Business Officer at Main Street Autonomy
William discussed how calibration makes sensor data more usable so that when computing data, multiple robots can perceive things similarly and can then behave similarly in a homogenous manner. Calibration enables hardware-agnostic machine learning, designed to function the same regardless of the hardware components being utilised. Mult-modal sensor technology is more reliable and safer has a variety of different sensors are individually fallible. Poor calibrations can manifest as poor perception, bad machine learning models, and a lack of homogeneity from robots due to the delocalisation of maps.
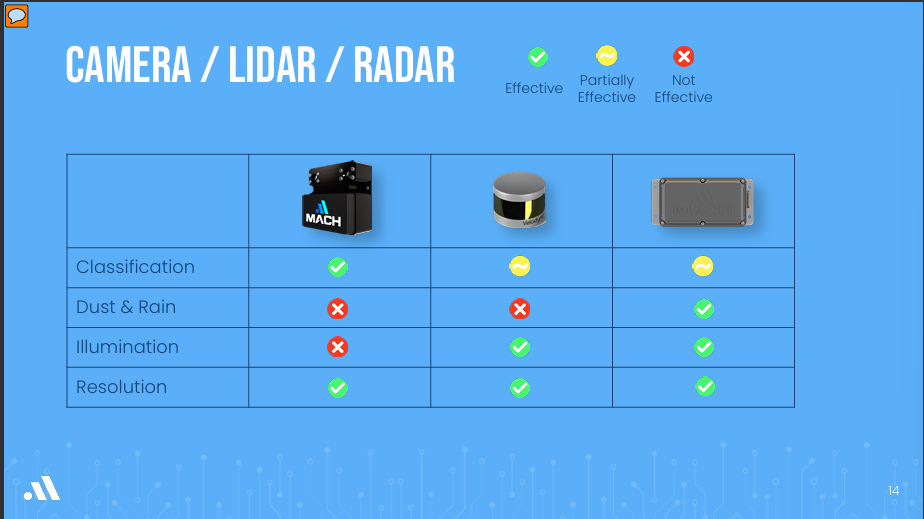
Deploying Off Road Autonomy at Scale
Colin Hurd, CEO at Mach, Inc.
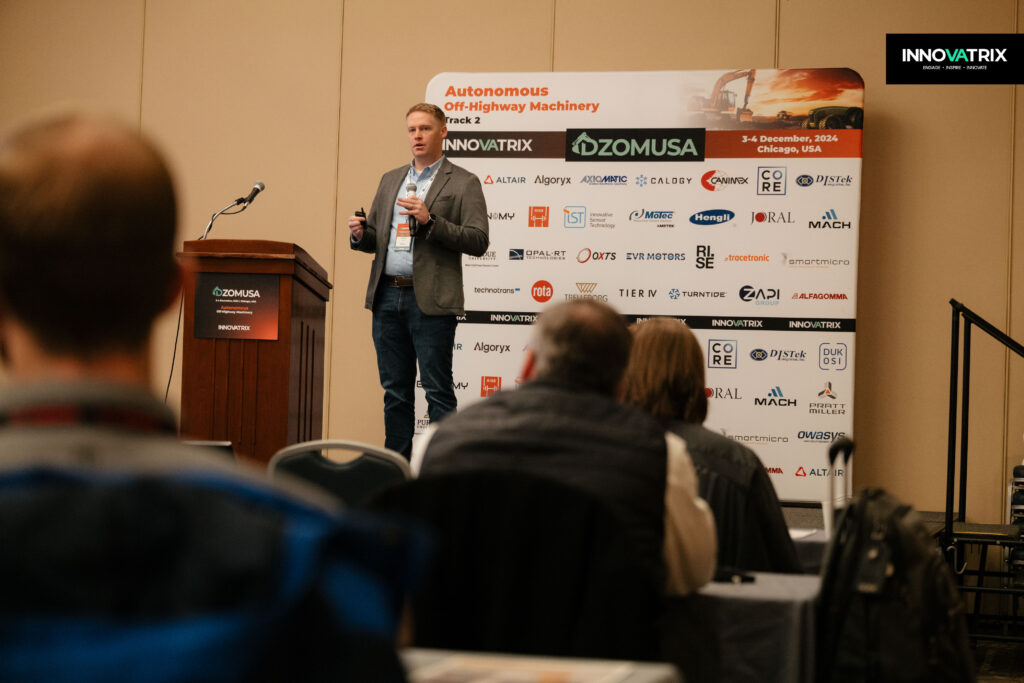
Autonomous vehicles being deployed at scale can reduce or augment labour required in certain jobs, avoiding the training costs and time involved in helping operators become proficient in a job in an industry with a 50% average turnover rate. A controlled operating environment greatly simplifies being able to achieve functional safety as variables can be managed, safety measures and strategies are implemented to ensure reliable performance and an assessment of potential risks and mitigation techniques has to be carried out. Phased array radar has multiple antennae that can transmit and receive signals independently, and the phase of each signal can be adjusted, allowing for advanced radar functionalities via constructive and destructive interference. Advantages include enhanced flexibility, dynamically adjusting the beam shape, direction, and scanning rate and the ability to generate multiple beams simultaneously, allowing for simultaneous tracking of multiple targets.
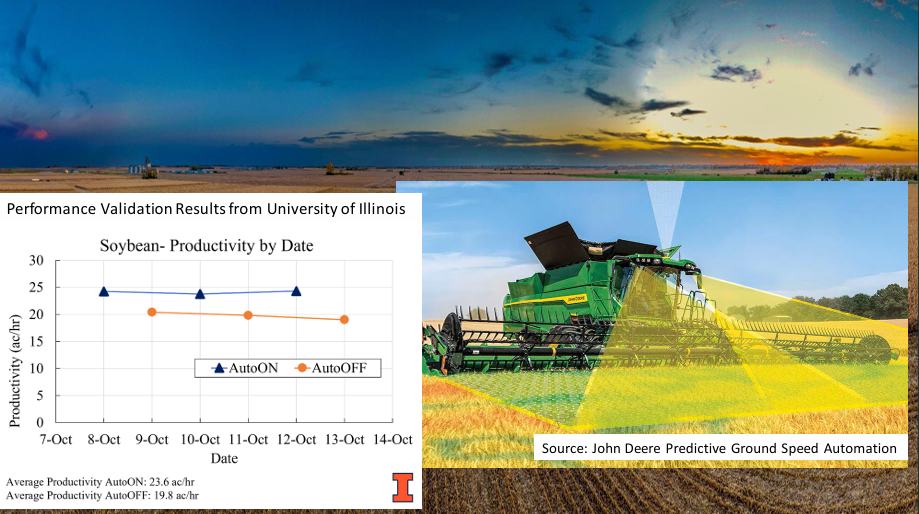
Automation in crop production systems
Cody Allen, Assistant Professor at the University of Illinois Urbana-Champaign

A method for growing crops involves preparing the land, seeding, and caring for the crops until they are harvested with the goal of producing a high-yield crop for the market. Processes and technologies are dependent on the crop type but for a crop like corn, automation can be integrated into the pre-planting work in the field by using autonomous vehicles for tillage job quality sensing. For the planting stages, automated tractors can be used and for applications of fertilisers, herbicides and pesticides autonomous machinery can be used to apply them over fields. The integration of autonomous machinery into the crop cycle leads to increased productivity.
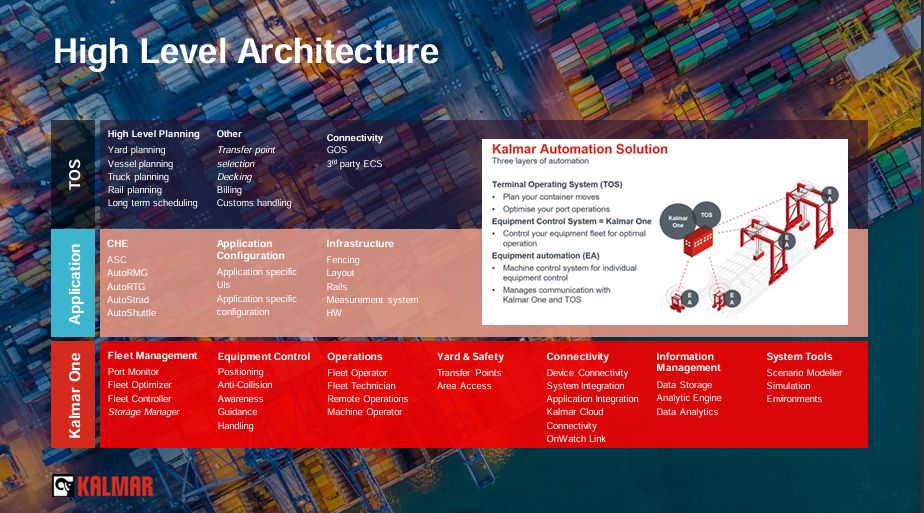
Automation in Marine Terminals
Mika Seppä, Head Automation Operations PMO at Kalmar
Kalmar’s offerings for marine terminal automation include the KalmarOne, maintenance and support, SmartPort, process automation, straddle carriers for end-to-end operations, straddle carriers for shuttle operations and Kalmar Insight. Kalmar’s collision warning system for the manual straddle carrier detects and avoids obstacles by using top frame sensors, bumper sensors, blindspot sensors. KalmarOne can be used for automated equipment control as a part of automated operations in a system architecture with a terminal operating system and equipment controls. Automating marine terminals increases operational hours, is more sustainable and efficient and improves health and safety.
Exhibitors
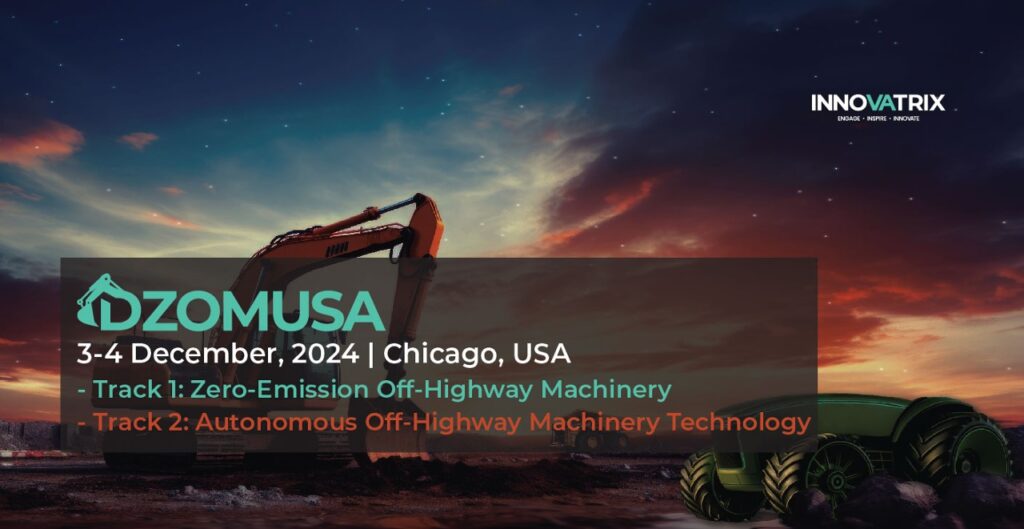
The DZOMUSA was supported by a wide range of companies who brought their teams to our exhibition hall and Innovatrix would like to thank them again for their support:
Alfagomma, Algoryx, Altair, Axiomatic Technologies, Calogy, Canimex, CoreM2M, DISTek, Dukosi, EVONOMY, EVR Motors, Hengli, IST AG, Joral, Mach, Motec, Opal-RT Technologies, Owasys, Oxford Technical Solutions, Pratt Miller, Purdue University, RISE Research Institutes of Sweden, RISE Robotics, Rota, smartmicro, technotrans, Tier IV, tracetronic, Trelleborg, Turntide and Zapi Group
If you want to attend our next autonomous machinery off-highway summit and have the opportunity to hear presentations like these and many more, join us for our European edition this May. Discover the latest innovations and trends in electrifying off-highway machines, meet with solution providers and hear talks from industry leaders, and attend the 4th Autonomous Off-highway Machinery Technology Summit taking place in Berlin, Germany on May 21-22, 2025.
For more information, visit our website or email us at info@innovatrix.eu for the event agenda. Visit our LinkedIn to stay up to date on our latest speaker announcements and event news.