The 2nd Battery Gigafactory Summit USA: Advances in Planning, Engineering and Operations took place from the 13th to 14th of November, with attendees from all over the battery manufacturing industry coming together in Nashville, Tennessee at the Margaritaville Hotel. The two day conference had a wide and comprehensive agenda that involved dozens of presentations from expert speakers, panel discussions, workshops and networking breaks.Ā
Our attendees discussed the challenges and innovations shaping gigafactories today, how to enhance efficiency, promote sustainable practices, improve air quality and fire safety within these facilities and the broader aspects of their design, production, planning, and construction.
This article will provide a session recap for those who didnāt get the chance to attend and serve as a reminder for those who attended.
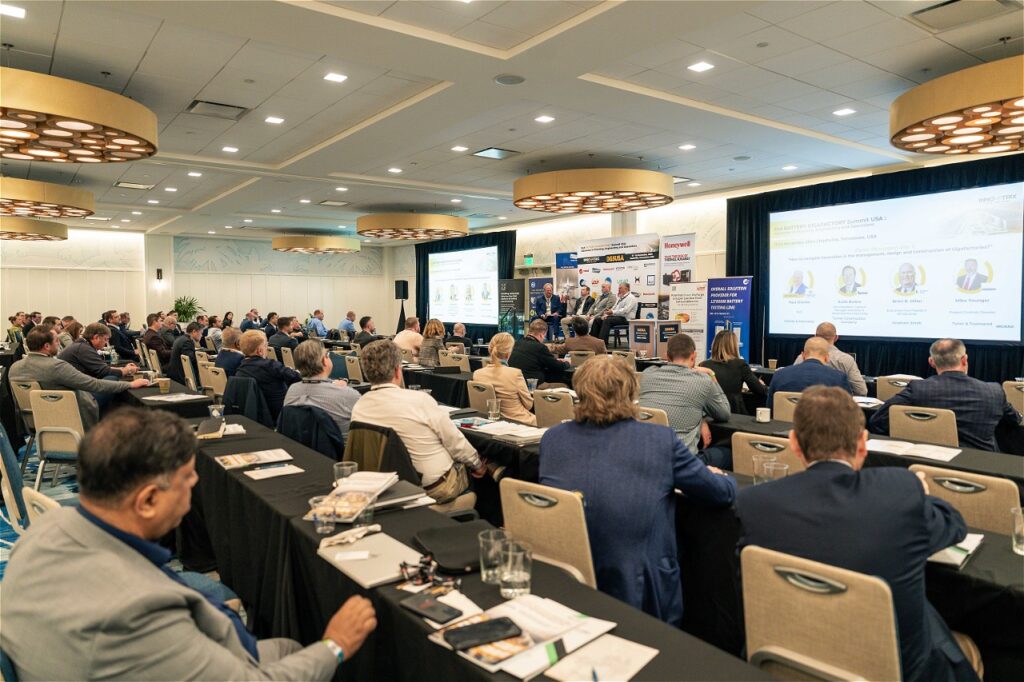
Day One
An Optimized Execution Strategy for the Design and the Construction of a Gigafactory
Jacob Matly, Global Director Battery Cell Manufacturing (Gigafactory) at Hatch
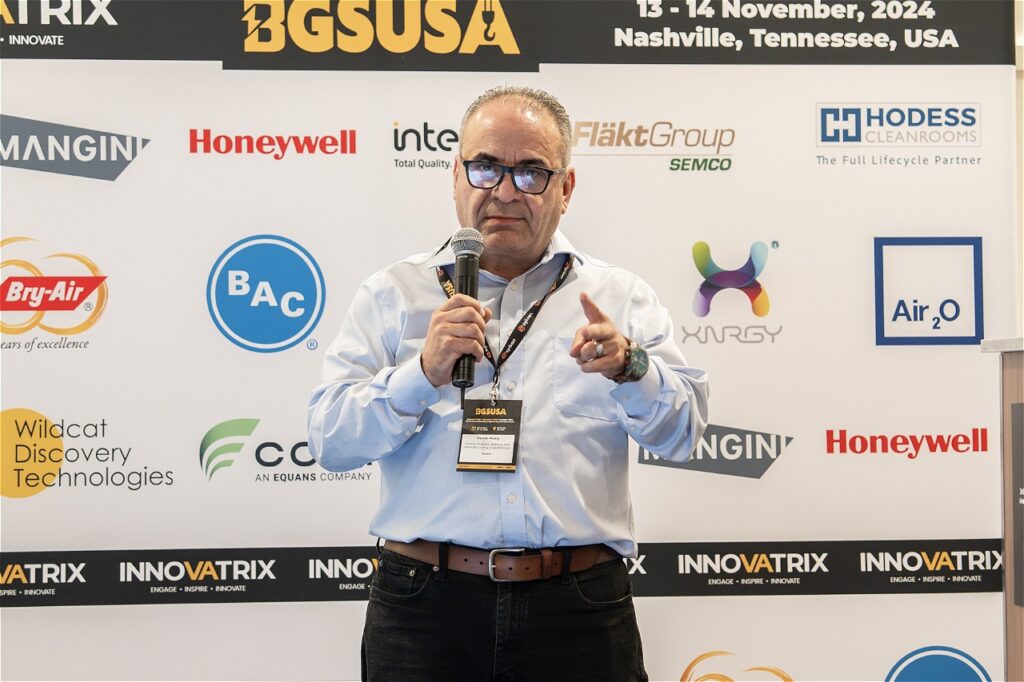
Jacob shared his insights on the CMAR (Construction Manager At Risk) contract model and its application in building gigafactories for lithium-ion battery manufacturing. He discussed the constructor engagement in the CMAR model and the methodology used to help ensure GMP. CMAR provides certainty of outcome, utilises qualification-based selection, provides design phase assistance and minimises change orders and unknowns, increasing predictability. However it is a new practice for gigafactories and would cause a culture change, making for a steep learning curve for those unfamiliar with the process, He argued for CMAR to be used as the execution model for battery projects as it provides cost certainty on the majority of CAPEX, provides benefits of EPCM model and engages Engineer and Contractor early on to progress design and plan execution.
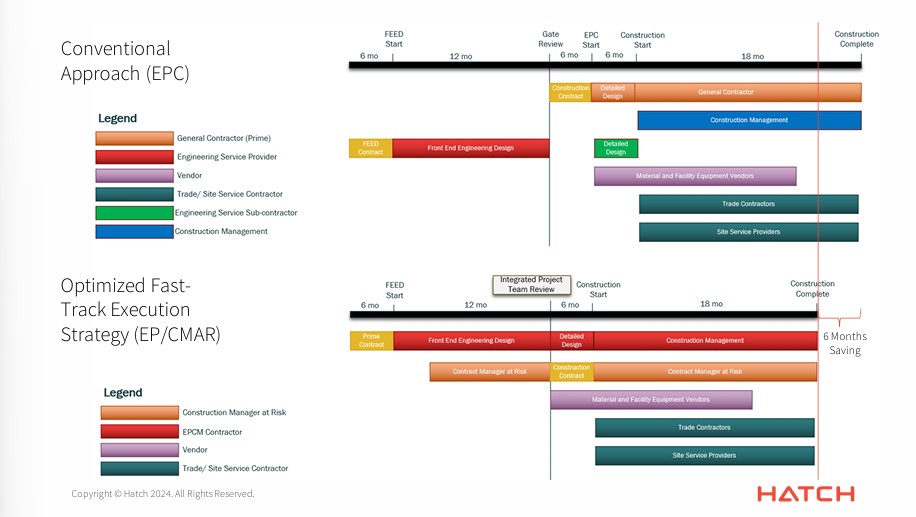
HVAC Procurement Complexities, Cost Reduction Strategies, and Systems Integration for Plant Decarbonization
Vickie Sims, High Tech Manufacturing, Market Leader at Trane Technologies
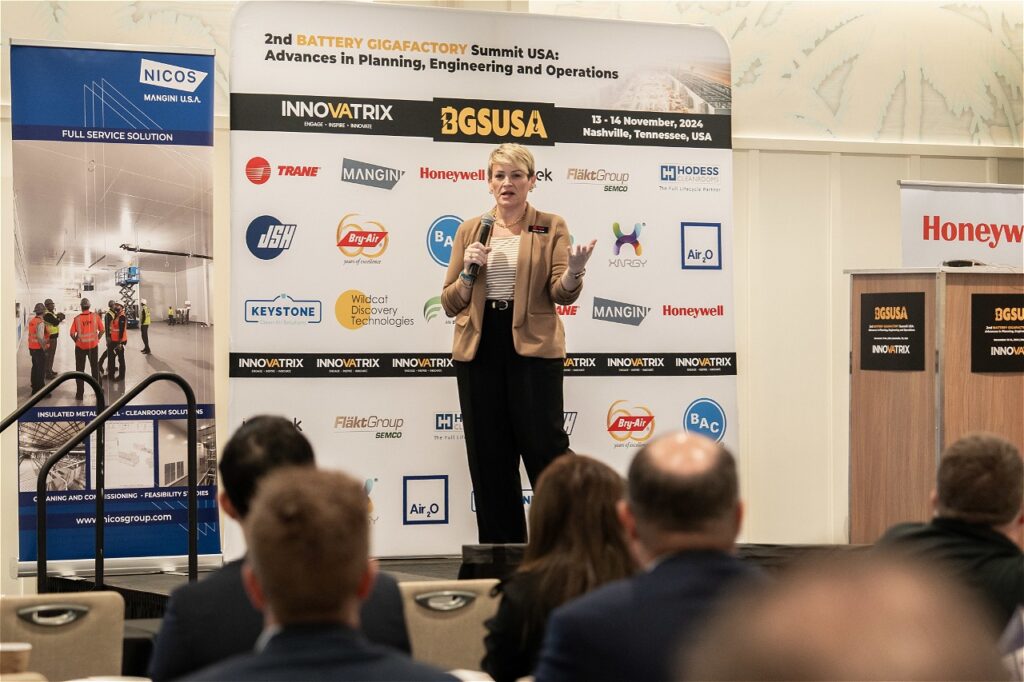
Vickie started her presentation by discussing the global growth of gigafactories worldwide, with over 200 predicted to be constructed by 2030. Gigafactories have an annual power usage equalling approximately 1.5 million homes and use 132 million gallons of water, with 43% of energy usage being directed to HVAC systems. She discussed three case studies where Trane Technologies helped two industries increase energy savings, pioneer sustainability and resolve production challenges. In a high-tech automotive parts manufacturer, ineffective HVAC had led to an uncontrolled IEQ that had quashed yield challenges and production quality issues. By using a chilled water system, modular design and advanced controls to identify trend data to prevent fix-on-fail cases, there was a saving of 575,000 kWh of electricity, >$30,000 annual energy savings and >423 tonnes of CO2 emissions reduced annually. In a semiconductor fab, Trane pioneered an industry-first>4500-ton heat recovery chiller, cutting natural gas use and saving water, resulting in a facility that achieves ambitious net-zero sustainability goals.
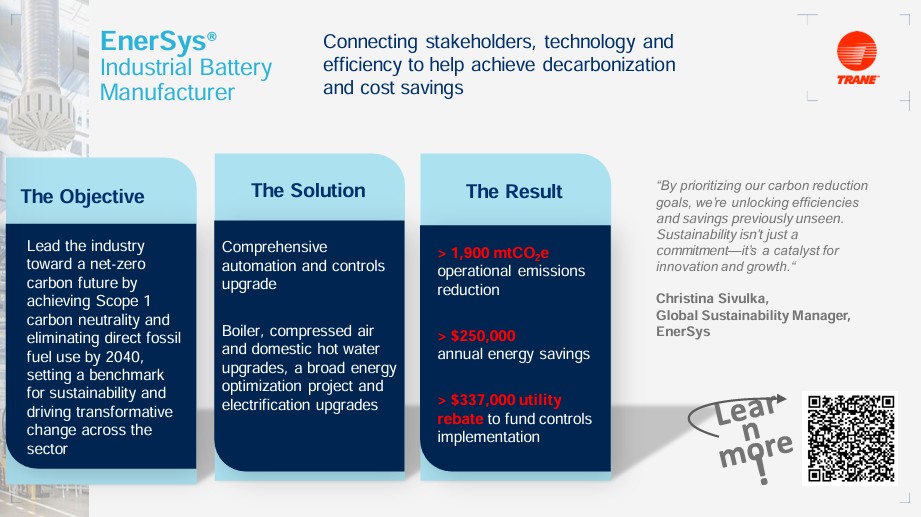
Digital DNA: Synchronizing Molecules to Machines to Enable Smart Gigafactories
Shailesh Upreti, CEO of C4V
He addressed the fact that while most gigafactory growth is enabled by duplicating what exists in the East (China, Korea and Japan), the waste generation, safety hazards remain a primary concern and a major restraint to market expansion in North America and Europe.
Shailesh and his colleagues have designed a prismatic cell that allows for 600 amps of power, offering the opportunity of modularity with its design. The smart gigafactory concept utilizes an intelligent manufacturing system that integrates artificial intelligence and machine learning, using gathered data āmoleculesā such as sales/transactions data, consumer data and battery component data and analysing them with AI to perform predictive monitoring that results in improved yields, predictive manufacturing and forward-looking smart decisions that increase profits.

Cooling GigaFactories with Sustainability Goals
Bill Williams, Global Director Business Development – EV Battery at Baltimore Aircoil Company
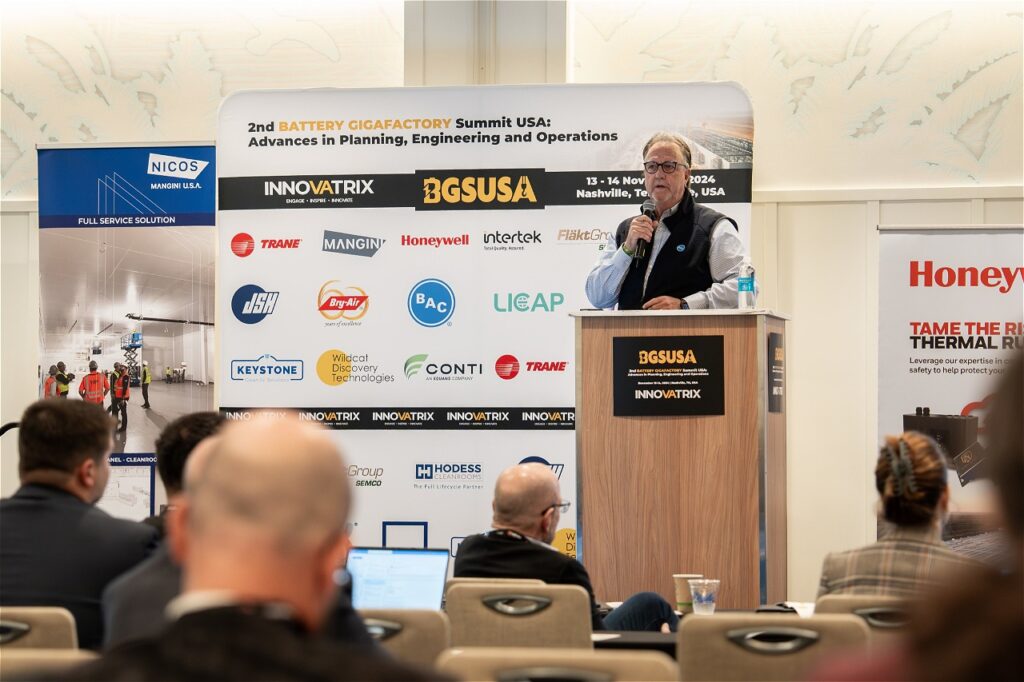
Bill covered the heat load split observed in battery manufacturing, identifying which processes were using the most energy relatively. He discussed the three major challenges for gigafactories, the issue of lower power usage while lowering water usage and reducing carbon emissions and meeting these sustainability goals despite aiming for lower operation costs. He discussed examples of existing projects, lower costs of installation and lower costs of maintenance. BAC technology can be used in a product mix that keeps both energy and water consumption down and minimises carbon footprint, utilising their extensive product portfolio and personnel to customize cooling solutions that work for every gigafactory.
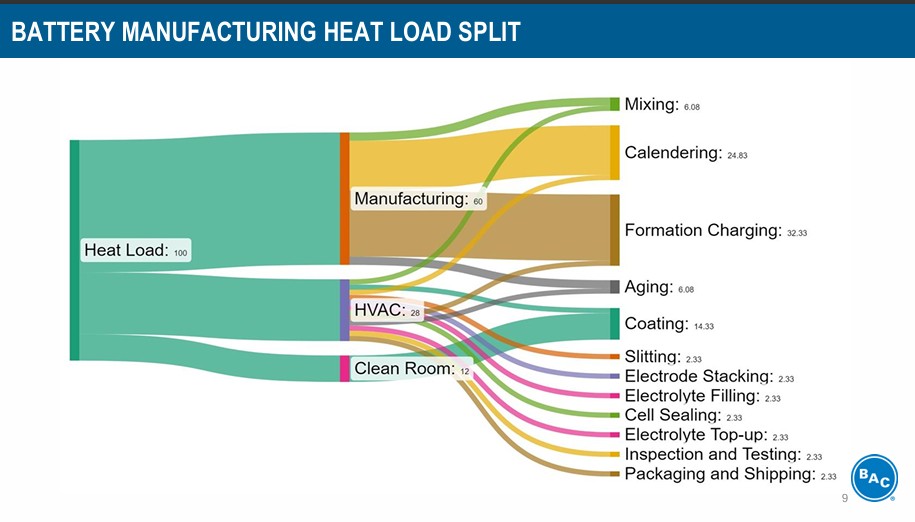
Systematic Problem Solving Techniques with Innovative New Technologies – how they can be applied to battery manufacturing processes
Humam M Alwan, Technical Program Manager Software X Quality Management at Stellantis
Humam shared the Stellantis practice of systematic problem solving that uses structured methodologies that efficiently identify and address root causes of complex manufacturing issues. The method first asks you to identify whatās happening rather than what is wrong, and consult meaningful data that leads to more information that can be used to pinpoint the issue that becomes knowledge which forms the basis of the convergent thinking used to find a solution. By using the process of elimination by ātalkingā to the parts and making decisions using statistical confidence, an engineer can arrive at a solution. He then shared how cutting-edge strategies and new technologies can be used to boost decision-making and problem-solving capabilities in dynamic manufacturing environments.
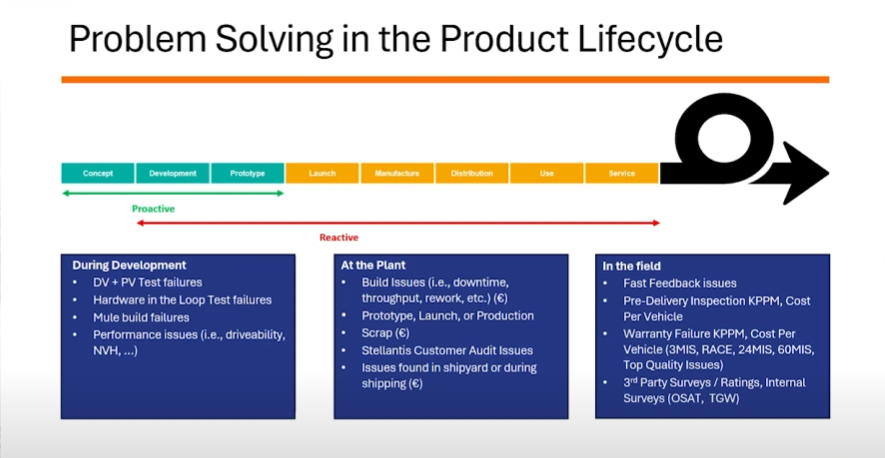
Cleanroom modular system approach in Gigafactories vs traditional IMP
Jack Szmanda, President at The Berg Group, and Mauro Cottafavi, Vice President at Nicos – Mangini USA
After providing a brief background on both their companies and their international collaboration and scope of work, Jack and Mauro stressed the importance of modular cleanrooms as the only real flexible solution for environmentally controlled areas and dry rooms in gigafactories. They explained the features available when selecting walls for cleanroom construction, comparing their panels versus traditional wall panels and discussed various case studies of cleanroom projects they have installed for their clients worldwide. They discussed how to scale walls above 10 metres for gigafactories and how to use integrated systems to meet the requirements.

What It Takes to Build a Smart Gigafactory?
Dr. Katharina Gerber, Engagement Lead for Battery Industry at Siemens
Dr Gerber began her presentation by covering the first step of creating a digital twin of a gigafactory, the design and validation stage. This first required planning the factory layout by creating conceptual and detailed layout designs that integrate equipment into a line in the context of the factory, then entering the process optimization step by defining the process requirements that drive equipment specifications and validating automated equipment and production capacities. A digital twin can use incoming data from sensors installed in the gigafactory to optimize processes within the digital model which then can be implemented in the operations of the gigafactory, creating more data and closing the loop. Dr Gerber also discussed Manufacturing Operations Management (MOM) and how Intra Plant Logistics (IPL) can optimize material usage for higher material turnover and increase flexibility and adaptability to
changing production demands. She explained how Enterprise Manufacturing Intelligence (EMI) can provide seamless and integrated data connectivity, contextualization between OT to IT and out-of-the-box solutions to create performance transparency and predictive analytics for Performance, Availability and Quality.

DRIF – Redefining Dehumidification with Novel Materials & Energy Efficiency for Giga Factories
Dr. Vijay Chaudhry, President of Bry-Air
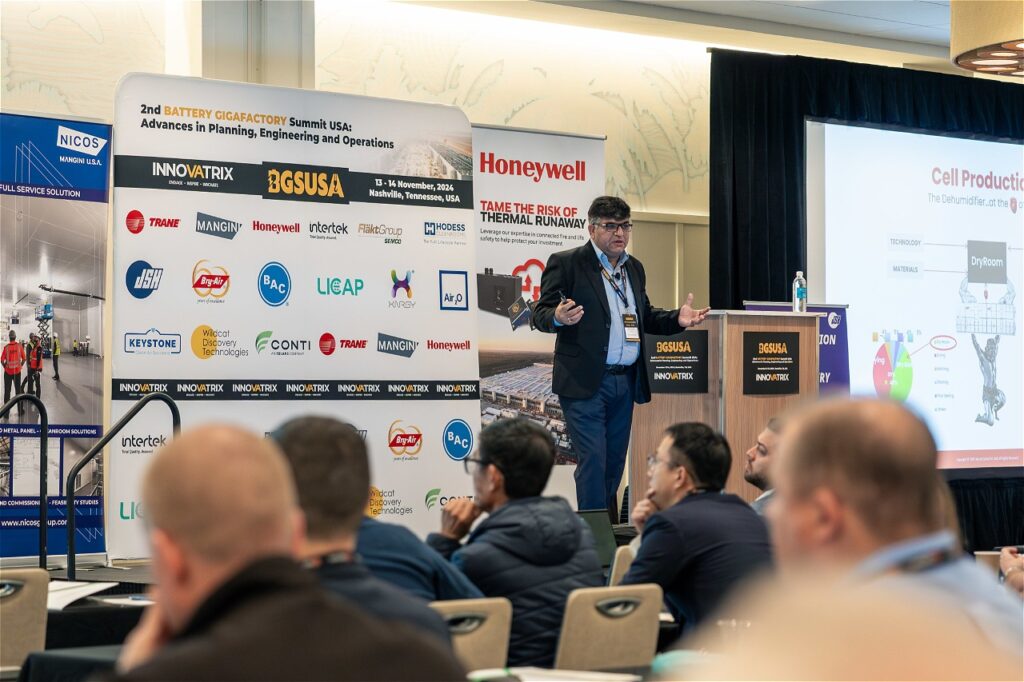
Dr Chaudhry introduced Bry-Air as the pioneers of the Rotary Silica Gel Dehumidifier and revealed their newest innovation for 2025, a new honeycomb rotor with special ānovelā adsorbent that outperforms traditional silica gel wheels by >20% and can slash overall energy consumption by another >50%. He explained how Bry-Airās Desiccant Rotors International Framework (DRIFs) are novel porous materials with bespoke structural frameworks that customise multivariate adsorbents which are application-specific. Their characteristics include being thermally economic, energy saving, fast kinetics, and having optimal working capacity. He also shared Bry-Airās solution for NMP recovery from cathode drying systems with an indigenously developed NMP/VOC concentrator. Recovering NMP can reduce hazardous and toxic waste and help recycle and reuse an expensive solvent, helping manufacturers be more cost-effective.
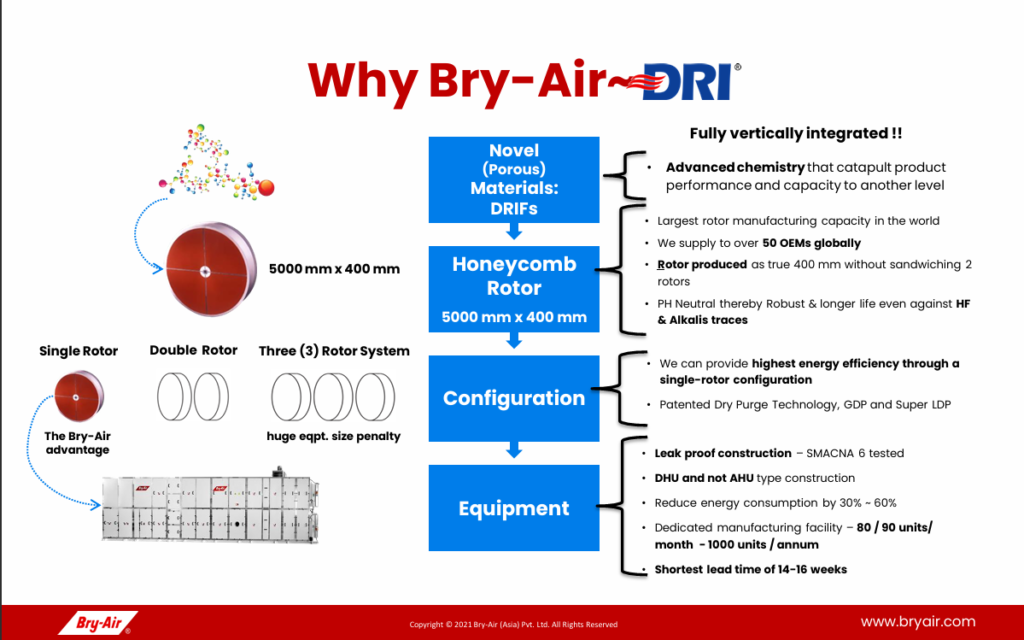
Transforming Battery Manufacturing with Activated Dry ElectrodeĀ® Processing
Chris Lee, Vice President of Business Development at LiCAP Technologies
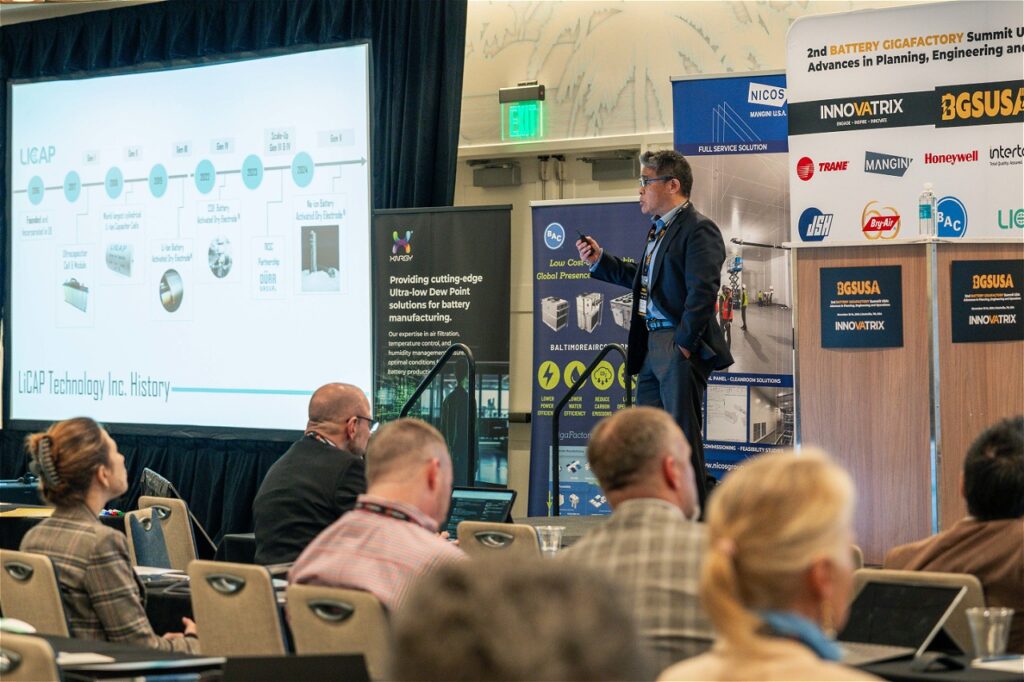
Chris covered the challenges of electrode production such as costs and use of toxic solvents and how LiCAPās Activated Dry Electrode process eliminates the need for drying ovens and recovery systems, resulting in significant savings in capital expenditures, energy use, manufacturing space, and carbon emissions. LiCAPās Activated Dry Electrode ProcessĀ® reduces the current āwetā processing steps from 5 to 3 by cutting out the toxic solvent step and instead following a process of mixing, binder activation then electrode film and then finally, the lamination step. The Activated Dry Electrode ProcessĀ® lowers CAPEX by 20%, energy usage by 70%, manufacturing footprint by more than 80% and carbon footprint by 70%. They can be utilised in a wide range of loadings – from EV to ESS applications with zero compromise on performance and manufacturing line speed.
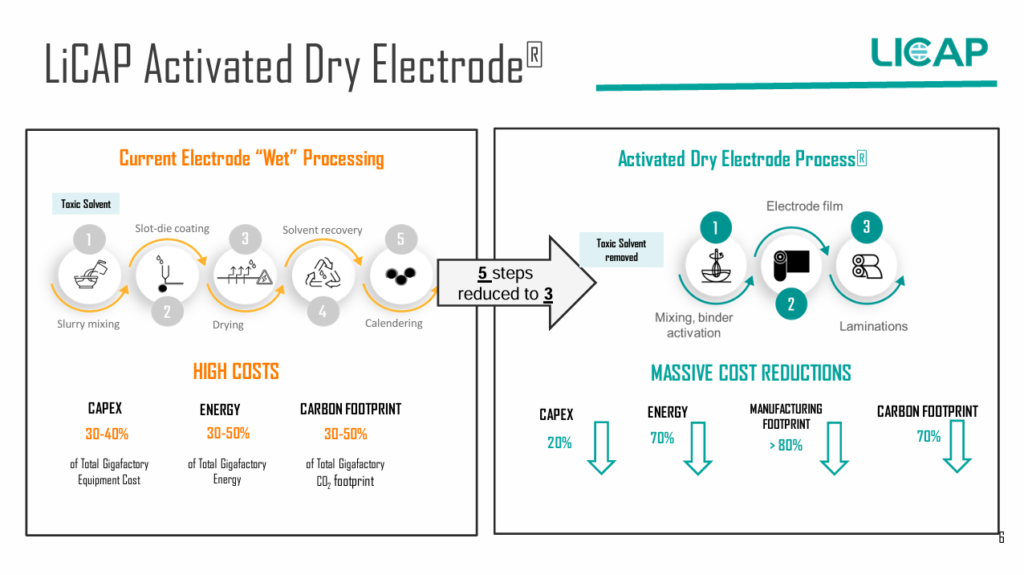
Keys to a Successful Clean/Dryroom Project
Mark McLelland, Group Vice President – Vehicle Manufacturing at Walbridge, and Blake Hodess, CEO of Hodess Cleanrooms
Mark and Blake gave a joint presentation on how to build a cleanroom and dryroom at a successful plant, identifying the key requirements and factors to know when constructing a gigafactory: dewpoint, particulate, room construction, people, airlock, exhaust, room height, air changes per hour, heat load and chilled water. They advised to clarify humidity requirements using dewpoints and checking permeability calculations for walls, floors and ceilings. When constructing a room or designing a layout, engineers must evaluate process conveyors, also critical to DHU sizing, to understand the number of openings, size of openings, rate, and speed of shutters used. When building a tight dryroom CFD modelling of rooms with process equipment layouts is necessary during design to verify that the rooms will serve their purpose. They also covered the use of ISO 14644-1 Part 1; Classification of air cleanliness to design cleanrooms and how cleanroom protocol after construction must follow ISO 14644-2 Part2: Specifications for testing and monitoring to provide continued compliance with ISO 14644-1.
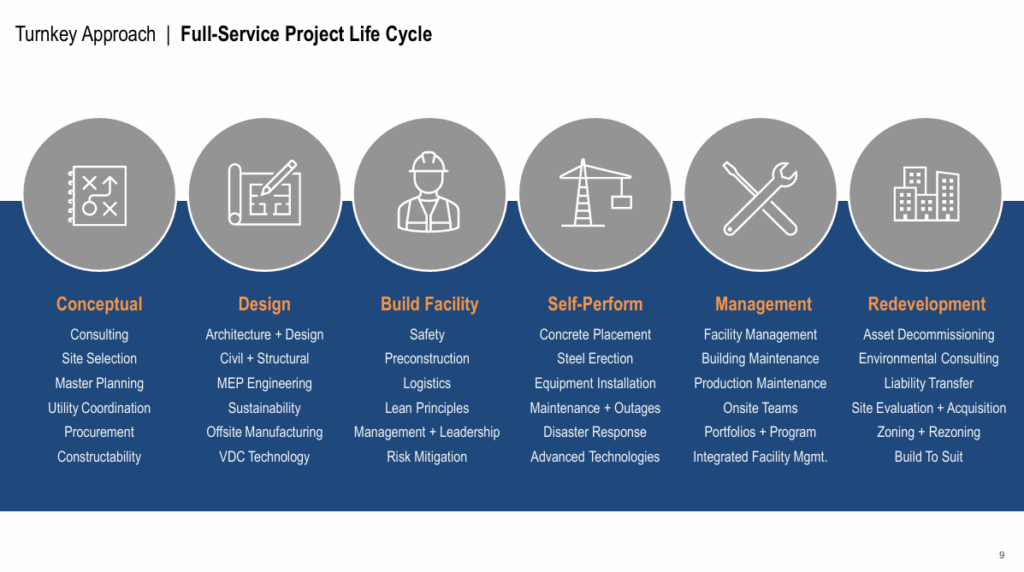
Construction Strategies for Gigafactories: Balancing Efficiency, Cost and Schedule
Scott Bulera, Vice President, General Manager Industrial & Advanced Manufacturing at Turner Construction Company
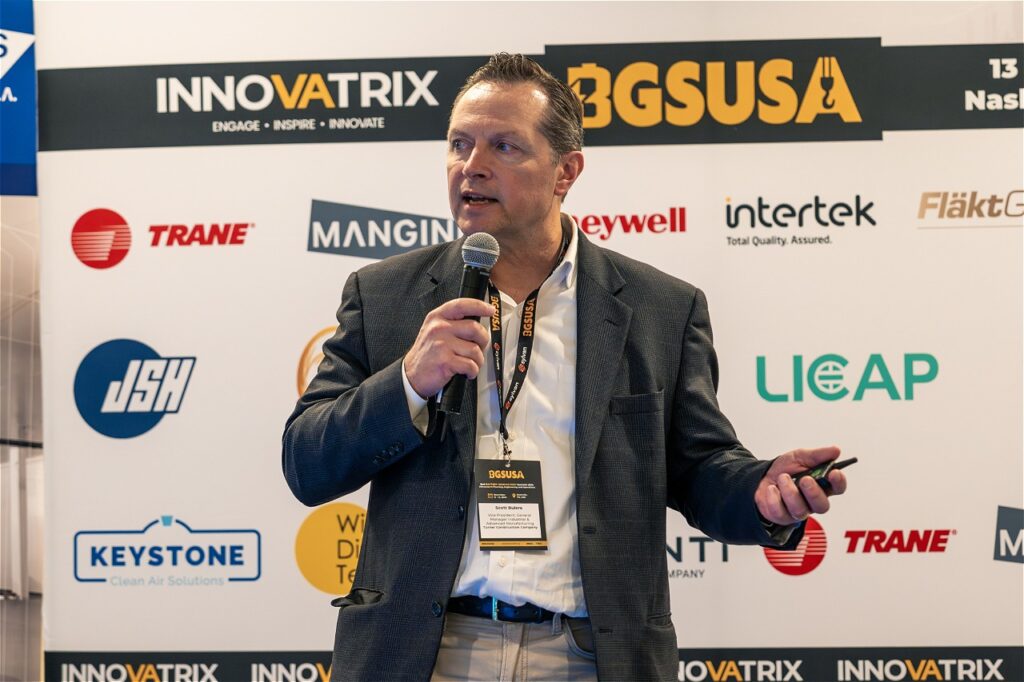
Scott covered techniques to streamline the construction process, reduce build times, and increase overall efficiency without compromising quality and methods to effectively control and reduce costs through innovative procurement strategies, technology integration, and lean construction practices. He identified the need to recognise the Critical Path before construction as streamlining is not possible if the team is not aligned on what is or is not critical. Scott shared his knowledge on how to expedite site selection and avoid schedule delays by demonstrating progress to investors and avoiding speed bumps such as rezoning and public utilities issues. Procurement strategies balance schedule with competitive pricing with progressive design and phased trade packages that culminate in a GMP. He also discussed using lean practices to control and reduce costs, a lean approach values those closest to the work and eliminates waste with continuous improvements.
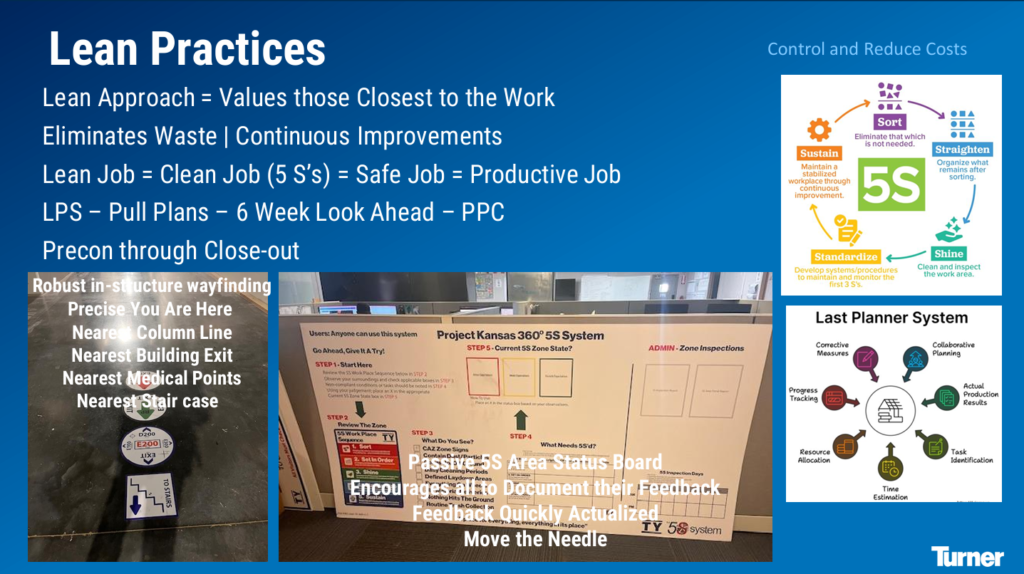
The Gigafactory Challenge – Ensuring Safety and Compliance in Your Builds
Gary Flom, Service Line Leader at Intertek
Gary shared his knowledge on satisfying the authority having jurisdiction (AHJ) – the organization, office, or individual responsible for enforcing the requirements of a code or standard, or for approving equipment, materials, an installation, or a procedure – by sending your best people to manage the relationship with them and connecting with suppliers or contractors that may otherwise be unfamiliar with U.S. Codes and Standards. He explained Intertekās capability to conduct preliminary design reviews (PDRs) outside the U.S., ensuring fewer issues when equipment arrives, preventing unwanted delays and providing AHJās with a PDR beforehand. Intertek provides an initial plan of how we will conduct our assessment of the factory and how we will organize all documentation for the AHJās review and coordinate with the AHJ to identify gaps, ensure appropriate resolutions, and validate code compliance on behalf of the factory.
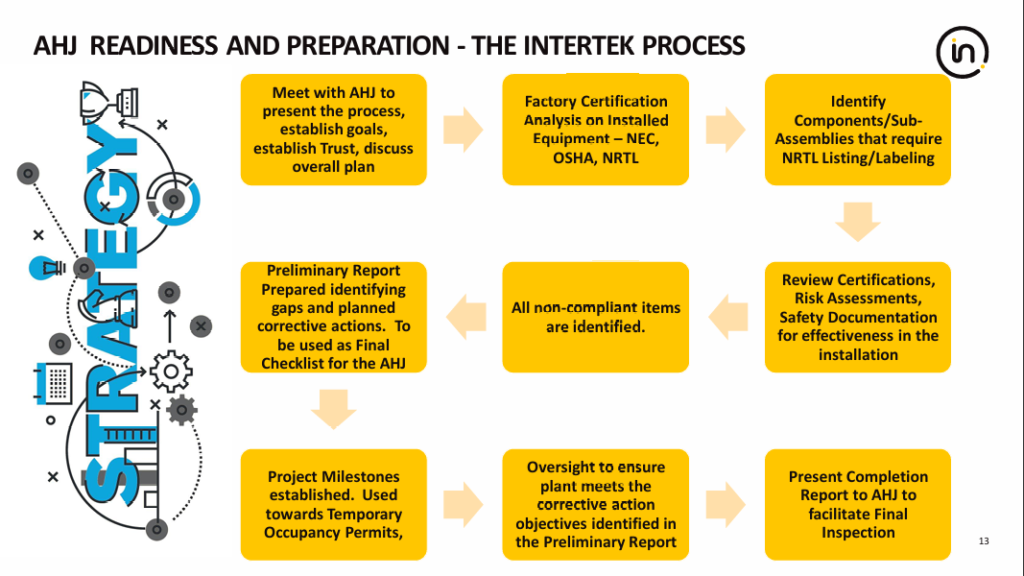
Day Two
Federal Programs, the IRA and other Incentives in 2025 and beyond
Jason Knapp, Managing Director at Capitol Energy Advocacy, LLC
Jason posited that the incoming Trump Administration will be far more prepared to take action on Day 1 than in the first Trump presidency, addressing the possible use of the Budget Reconciliation Process to pass major legislation without bipartisan support and the Congressional Review Act to review and overturn federal agency regulations, making use of executive actions and using presidential authority to impose tariffs. The administration will however have limited power to change any of the IRAās protected provisions such as the Clean Vehicle Tax Credit, Clean Energy Investment Tax Credit and Clean Fuel Production Credit. In his previous presidency, Trump imposed tariffs on imported products such as steel and aluminum, Chinese imports and solar panels and he promised to increase all tariffs by 10% (60% for Chinese imports) and levy a reciprocal tariff policy on other countries.

Net Zero Battery Cell Formation Turnkey Solution
Chris Nengka Li, Manager at JSH Power System R&D Department, Shenzen Jingshine
Using a case study of JSH-delivered projects Chris shared that cell formation and capacity grading are responsible for 40% of the total energy consumption of battery manufacturing, with the primary energy consumption being heating, cooling and electricity conversion. By using next-gen formation machines for the cell formation process, the efficiency has improved by 80% as well as removing the need to heat a dryroom as its all-in-one. JSH also has a 700V HVDC capacity grading machine that also increases system efficiency thanks to the direct conversion of electricity and water cooling. Chris covered the 25GWh production line construction and implementation, production safety and new technology, Net Zero microgrid solutions and flexible AGV replacing some fixed logistics lines.
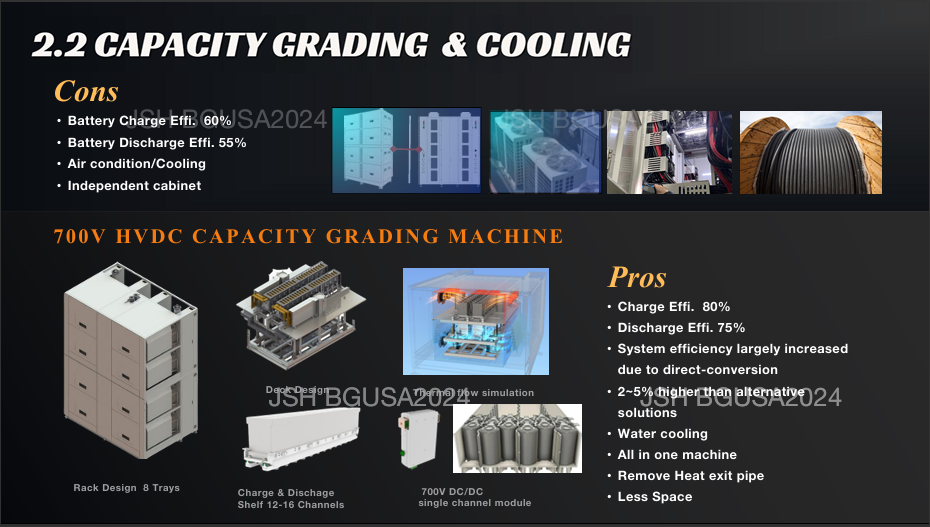
How to Prevent Thermal Runaway in Lithium-Ion Batteries
William Sudah, Industrial Fire Safety Consultant at Honeywell
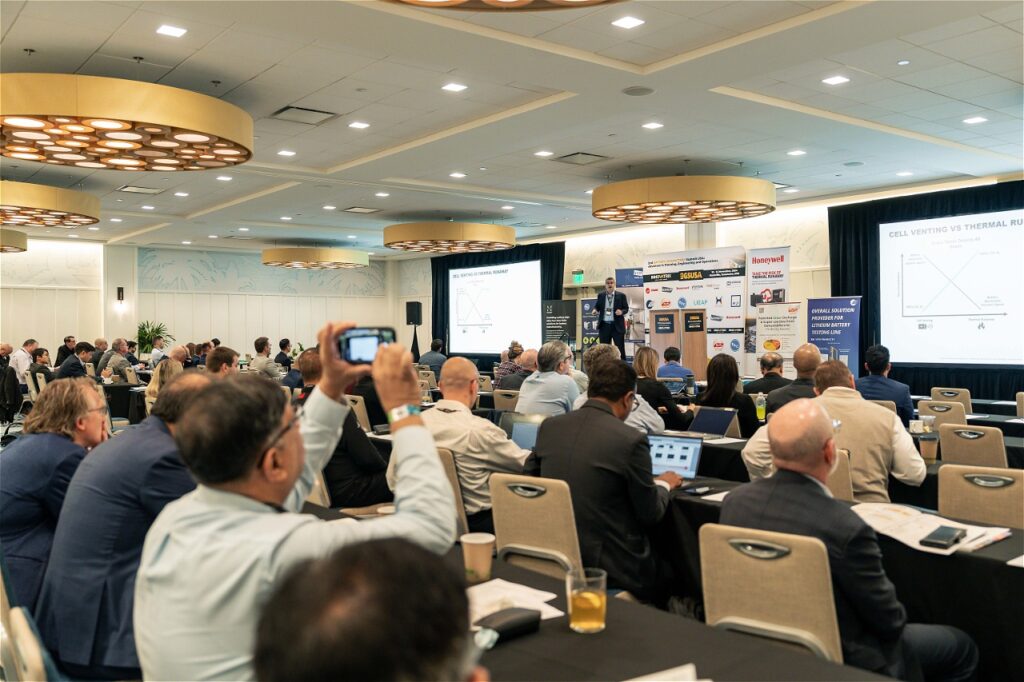
William recapped Li-ion battery thermal runaway, indicating the risk of how the exothermic reaction occurs and the 4 stages that can be identified to help prevent any fires: Stage One Abuse Factor, Stage 2: Off-Gas Generation, Stage 3: Smoke Generation and finally, Stage 4: Fire Generation. Li-ion tamers specialize in detecting early off-gases released from lithium-ion batteries prior to thermal runaway, quicker than conventional detector response which was 13.1 minutes slower. Off-gas monitoring can enable mitigation of battery failure and enable thermal runaway prevention. Cell formation, ageing and storage pose a very high risk to flammability due to the chemicals being used and the arrangement of the cell packs so a VSDA gas detector is used that does 24/7 active sampling and detection and is combined with a fire sprinkler system.
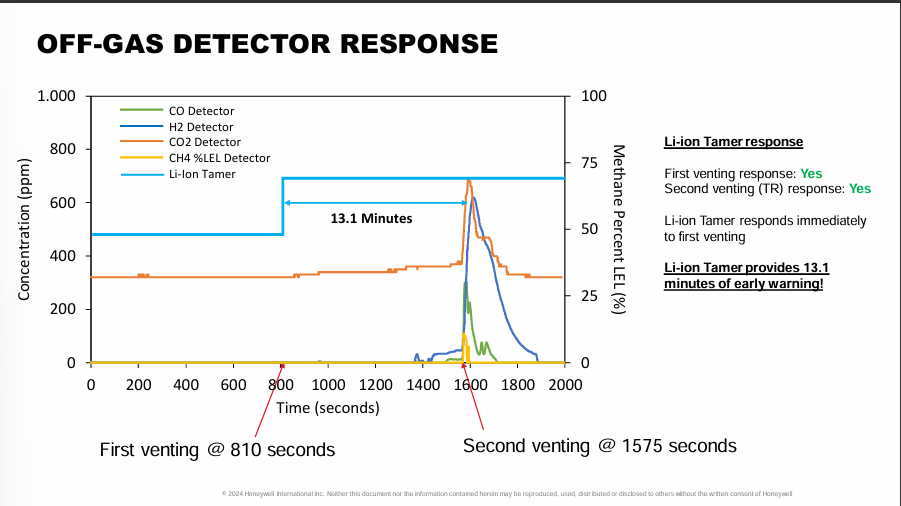
Tools Weāre Putting in the Toolbox to Prepare a Large EV Factory for Startup
Mary Jo Press, Chief Safety Officer at HMGMA (Hyundai Motor Group Metaplant America)
Mary Jo discussed hazards on site and within operation at the Hyundai Metaplant such as cells, their manufacturing materialism, devices in-transit and vehicles with installed batteries. She shared how emergency personnel are on staff with 14 EMS/Fire 3rd party responders on 3-24 hour shifts, 2 EHS emergency management staff and on-site security and dispatch to ensure safety. She also shared the physical resources being utilised such as UTV response vehicles, enforcer agent suppression systems like cop-poly water tanks, Waterax Striker 3 fire pumps, fire blankets and extinguishers. The plant has an EV fire manual prepared as well as an AGV fire response and an emergency procedure that covers all types of accidents. The plant has reciprocal agreements that encompass process flow for the management of issues in connecting bridges with conveyance tunnel suppression equipment.
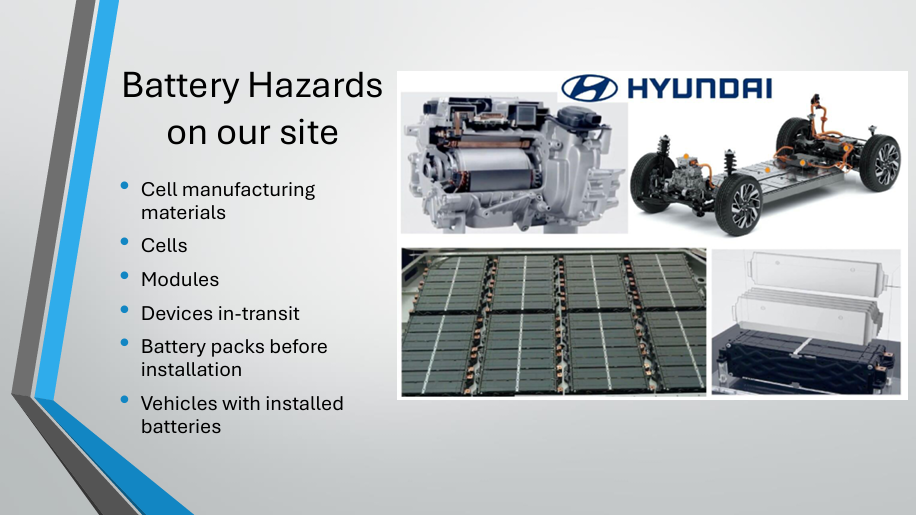
XNRGY- Custom AHUās Low Dew Point for Battery Dry Rooms
Art Doramajian, Director of Engineering – Battery Plants and Victor Yeramian, Business Development Director, at XNRGY Climate Systems
Art and Victor discussed the custom AHU offering with LDP for dry rooms, quality control AS built demo unit for dry rooms, scalability for LDP units over 700K sq ft manufacturing and factory startup and commissioning onsite. They covered how the fan array bank controller in their custom AHU offering provides a single point of control to fully utilize the operational savings and diagnostic benefits and reduces system installation and commissioning times with integrated automation. The Xmc Controls Solution provides clients with a senior team with extensive experience and turn-key factory commissioned systems with custom āfull-stackā controls tailored to customer-specific operational needs and site vocabulary.
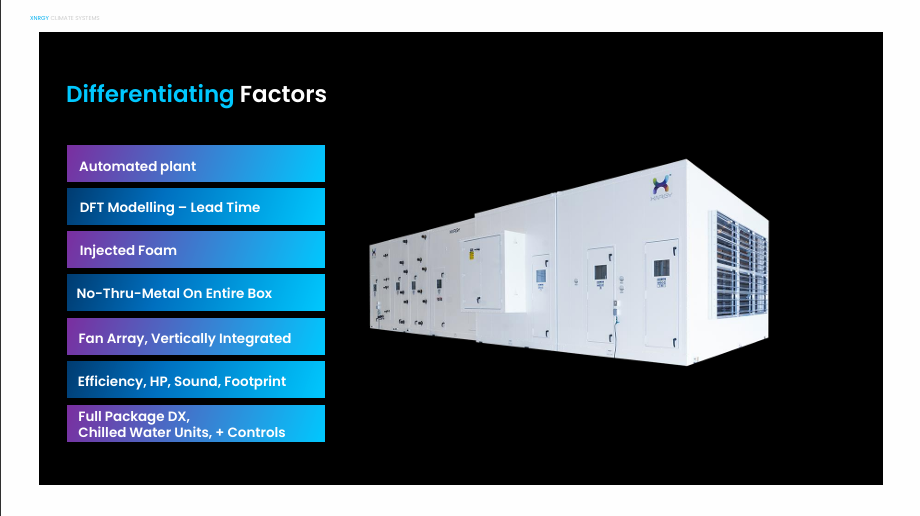
Fire response and strategies for BESS and EV fires
Kathleen McCaffery, CEO of McCaffery Consulting and Training and former Tesla Global Fire Liaison
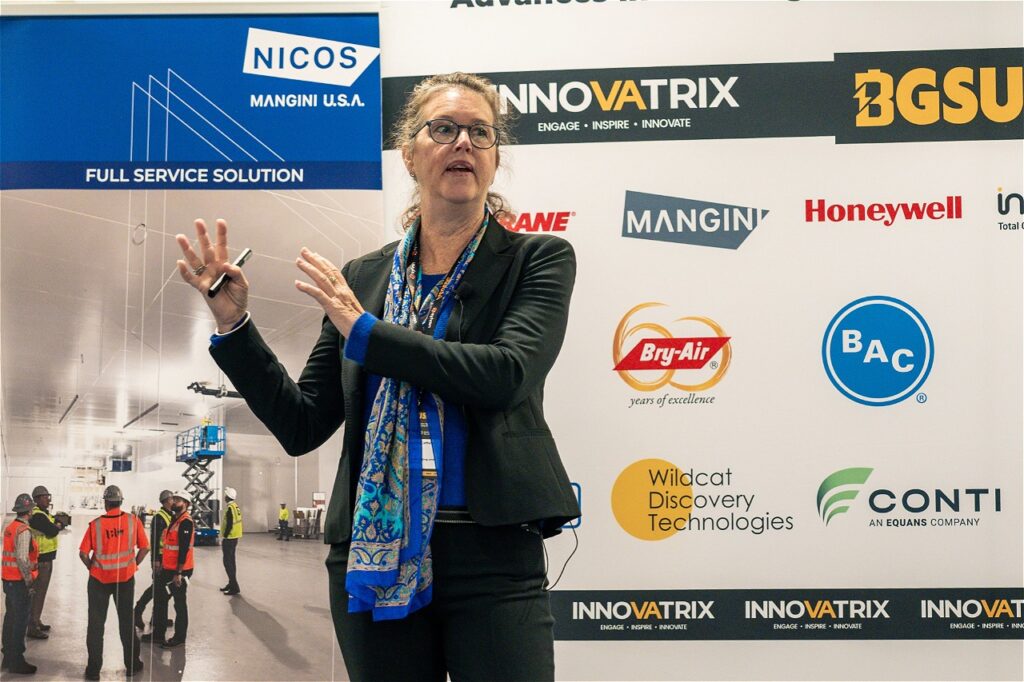
Kathleen began her presentation with recapping 11 major fires that have occurred in the energy storage industry since September with the conclusion that a relationship must be established with the local fire department from the start of construction. She recommends establishing an isolation area when building a lithium battery manufacturing plant to prevent fire spreading and keeping civilians away from toxic fumes in case of an emergency. Damaged batteries must be stored at least 1- feet away from other combustible materials and all fire suppression equipment should be easily accessible. Specific design features such as isolation areas and evacuation doors for equipment should be utilized during the pre-construction phase.
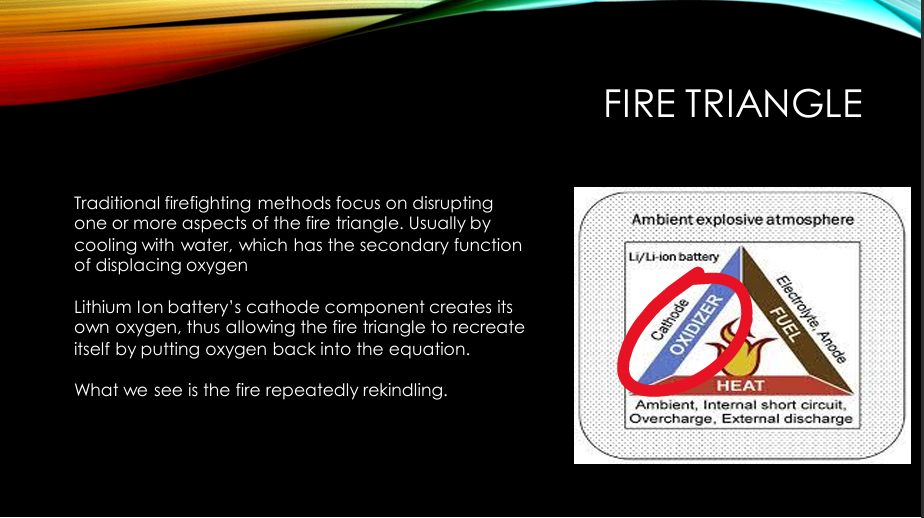
The Challenge of Energy Efficient Dehumidification for Gigafactories
Tom Rice, President & CEO of Gold Sponsors FlaktGroup SEMCO
Tomās presentation compared and contrasted different dehumidification approaches utilized in ultra-low moisture applications, the Ascendant, the GigaDry and the GigaDry+ that are able to meet ultra-low humidity requirements. Active desiccant wheel systems are the most cost effective way to meet ultra-low humidity requirements, able to achieve dewpoints as low as -70°F / -57°C with conventional chilled water and heating systems. They have the ability to tightly controlled dewpoints with customized DDC controls, sensors and algorithms. Low dewpoint air effectively cycles moisture between 95% and 5% relative humidity (RH) and maintains temperature stability and low heat transfer. The heated regeneration airstream (140°F-285°F) can use a combination of hot water, steam, gas burner, or waste heat to remove relative humidity.
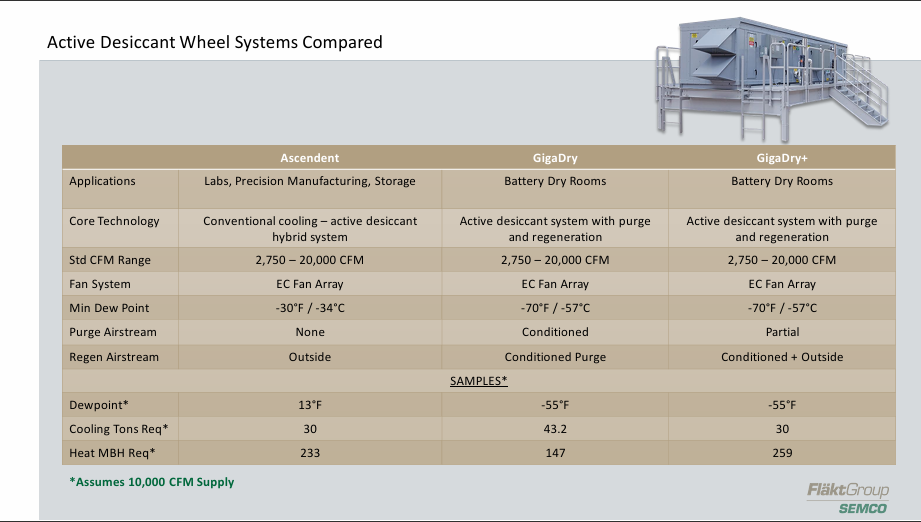
Factory Design Considerations for Different Battery Chemistries
Matthew Mendoza, Sr. Program Manager at Lyten
Matthew prefaced his keynote with the news of Lyten acquiring assets to accelerate US production of Li-S batteries as well as the announcement of Lyetn planning to build the worldās first Li-S battery gigafactory in Nevada. Matt discussed the advantages of Li-S batteries like being nickel/cobalt/graphite-free, ensuring a fully domestic supply chain. They use abundant, low-cost materials like sulfur, carbon, solvents that are inherently safer due to unique conversion chemistry and at maturity, 600 Wh/kg and 800 Wh/L possible. Lytenās Li-S cell architecture uses nanostructured 3D Graphene⢠that mitigates polysulfide shuttle and has high conductivity for high charge/discharge rate. He compared 4 different manufacturing processes (electrode, pouch assembly, formation and cylindrical assembly) and covered optimizing factory design for different Li-Ion chemistries (NCA, LFP, Li-S, etc.), process differences that impact current practices in Factory Design and Construction and progressing through factory design with a brand-new chemistry and the key considerations involved.
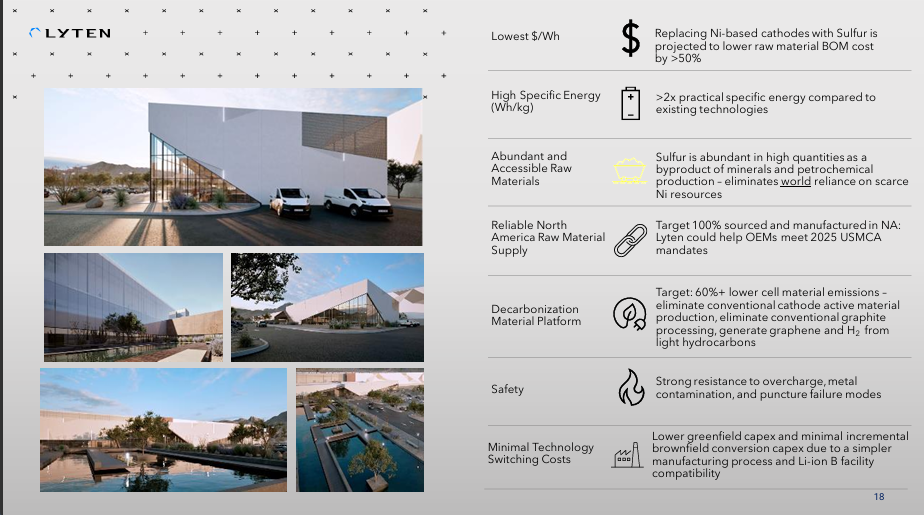
Scaling Battery Production for the Future of EVs
Evan Horetsky, Global Chief Development Officer at AESC
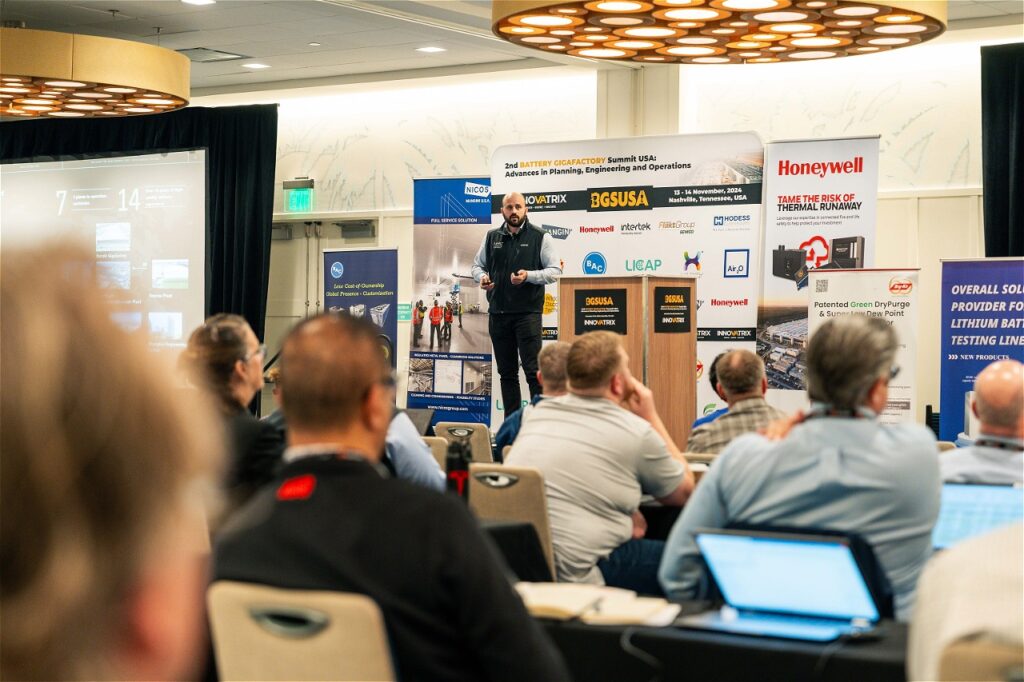
He recapped technological innovations in Gigafactory Design, discussed key challenges encountered during the planning, construction, and operation of multiple Gigafactories, including site selection, infrastructure development, and the integration of renewable energy sources, and how these challenges were addressed to meet the growing demand for EV batteries. Globally, the world fails at delivering capex with approximately 95% of all capital projects underestimating the costs incurred and the delays that they will face with green growth companies facing additional challenges. The challenges facing cleantech expansion and gigafactory growth are talents and knowledge, supply chain, the facility itself and geopolitical risks. AESC has a diversified product solution enables AESC technology competitiveness and to serve a variety of OEM requirements, access to visionary experienced experts and global talents, is recognized by world-class OEMs and has strategic cooperation with Top 10 of the world’s leading ESS Integrators by strong product and global delivery capacity.

Electrovayaās US Manufacturing Expansion
Raj S. DasGupta, CEO of Electrovaya
Raj gave his keynote on his companyās expansion into US manufacturing with their new factory in Jamestown, New York. He aims to produce batteries with a longer lifetime with their Infinity Technology that offers the highest cycle with over 4X the life of typical batteries of the same chemistry, improving safety with their proprietary ceramic separator membrane that significantly improves safety and power heavy duty applications like material construction & mining equipment. The Jamestown facility will be an advanced lithium ion battery manufacturing cell, module and pack facility and will produce Electrovayaās proprietary lithium ion ceramic (Infinity series) cell technology. The facility will increase Electrovayaās manufacturing capacity and has a strong financial return profile as well as increase Electrovayaās capabilities to support exports.
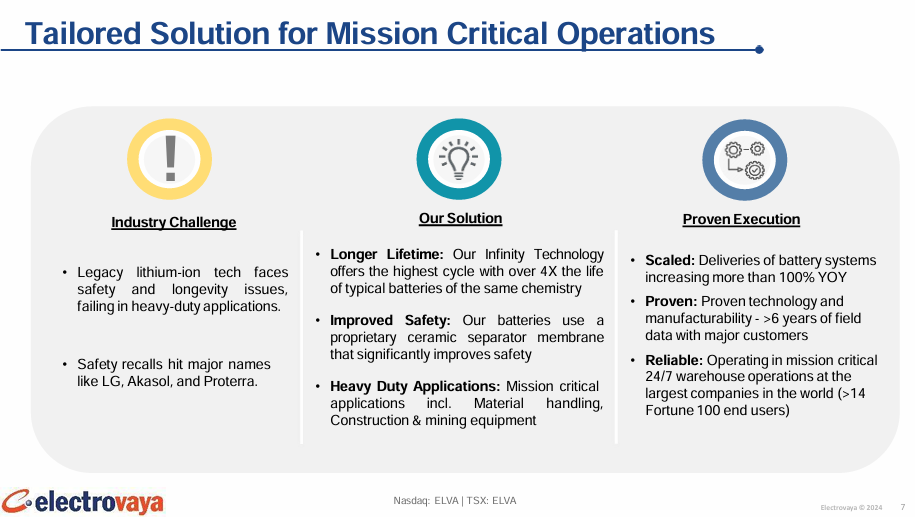
Sponsors
The 2nd Battery Gigafactory Summit USA was supported by a wide range of sponsors who brought their teams to our exhibition hall outside our conference room and Innovatrix would like to thank them again for their support.
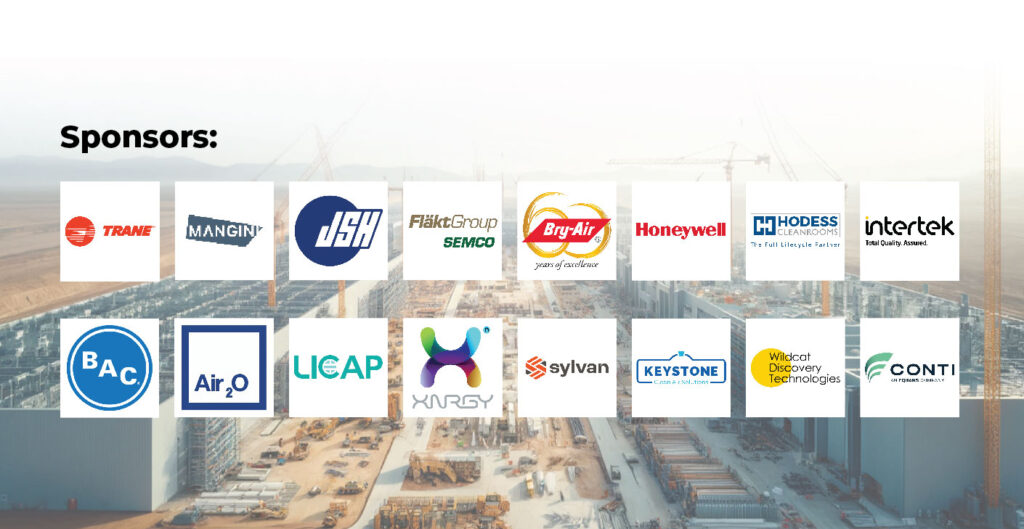
If you want to attend our next gigafactory summit and have the opportunity to hear presentations like these and many more, join us for our European edition this May. Discover the latest innovations and trends in gigafactory technology, meet with solution providers and hear talks from industry leaders, attend the 3rd European Battery Gigafactory Summit: Advances in Planning, Engineering and Operations taking place in Berlin, Germany on May 14-15, 2025.
For more information, visit our website or email us at info@innovatrix.eu for the event agenda. Visit our LinkedIn to stay up to date on our latest speaker announcements and event news.